Журналисты «СТРОЮ и ремонтирую» вникали в процесс производства дверей на фабрике «ОПТИМ» в городе Светлом.
Текст: Андрей Забелкин
Фото: Роман Городко
Только мы входим в цех № 1, как станки останавливаются, гаснет свет, рабочие покидают помещение. Неужели появление журналистов вызвало такой эффект?
– Да что вы, – улыбается директор по маркетингу фабрики «ОПТИМ» Михаил Колчин. – Просто пришло время обязательного производственного перерыва. Кто-то курить пошел, кто-то чайку попить, другие просто наслаждаются видом на морской канал. Но через пятнадцать минут все вновь завертится.
На коврики не наступать!
Мы же во время перерыва наслаждаемся запахом дерева в цеху, рассматриваем штабеля фанеры, бруса, полотен и других заготовок. Но вот оператор Александр Кузькин запускает распиловочный станок. Он способен принять сразу до 20 листов заготовленного материала, из которых выйдет приблизительно 50 дверей. Оператору надо на компьютере ввести нужную программу, оптимизировать расход материала, остальное сложный агрегат делает сам. В конечном итоге на выходе из станка появляются прямоугольные заготовки из ДСП, МДФ, ХДФ или другого закладочного материала.
Затем между ними укладываются картонные соты (они, кстати, выдерживают давление 20 кг/кв. см), трубчатая ДСП или, например, полнотелый противопожарный наполнитель. И мощный пресс превращает конструкцию в дверное полотно. Впрочем, это еще необработанная заготовка.
Инженер-технолог Юлия Руф ведет нас дальше по цеху и по ходу дела поясняет:
– В технологии производства дверей очень много нюансов. И все они, безусловно, важны. Только на кашировальной линии происходят десятки процессов. Желирование, форматирование, склейка, торцевание, технологическая сушка… Боюсь, вы только запутаете своих читателей, если углубитесь в детали. Давайте я вам лучше наш фрезерный станок покажу. Только на коврики перед станком не вставайте – остановите процесс.
Фрезерный станок – не менее сложный и громоздкий, чем распиловочный. В него загружается сразу несколько полотен, оператор задает программу, и фрезы начинают выводить на фасадах узоры – филигранные и безупречные. Понятно, что дверь с таким рисунком – спецзаказ.
Рубашка… из шпона
Вообще-то практически с самого начала процесс производства дверей мне стал напоминать некое швейное производство. Тут раскроили, здесь сшили, там приклеили, наметали, сделали вытачку и т. п. Как уже говорила Юлия Руф, очень много мелких, но важных деталей. Но когда мы дошли до рубашки…
Рабочий Виктор Бегешко делает выкройку из шпона. Из нее-то и должна быть «сшита» рубашка, как ее называют сами специалисты. А «шьет» ее уже Ирина Валейко. Ловкими движениями рук рубашка превращается… в идеальное натуральное деревянное покрытие для филенчатой двери.
– Отталкиваясь от фактуры шпона, мы можем нанести его в разных вариациях. Например, сделать прямой рисунок или боковой. Но мне больше всего нравится «елочка», – говорит Ирина.
В следующем цеху фабрики «ОПТИМ» двери подготавливают под покраску. Часть продукции, ту, что с фактурой попроще, готовят машины. А вот, например, двери, прошедшие обработку на знакомом нам фрезерном станке, обрабатывают вручную.
Одни работники цеха шлифуют двери, другие наносят грунтовку или изолянт. Затем после очередной проверки ОТК — вновь шлифовка, вальцовка.
В цеху, разумеется, пахнет краской. Однако на одном из участков – запах другой. Больничный. А из очередной конвейерной линии вырывается голубоватый свет.
– Это ультрафиолетовая сушка, – поясняет технолог цеха Галина Вавилова. – Несколько ламп сушат продукцию с разной волновой частотой. В результате мы получаем не только готовую к покраске продукцию, но и изделия, устойчивые к солнечным лучам. Такие двери не будут выгорать на солнце.
На вкус и цвет
– По желанию заказчика мы можем подобрать любой цвет, оттенок или их сочетание, – говорит лаборант-колеровщик Евгения Иванова. – Платина, золото, серебро, натуральные древесные цвета – все есть в нашем распоряжении. Разумеется, к колеровке подходим основательно, поэтому брака практически нет.
Из лаборатории направляемся в цех покраски. И простите уж за еще одно сравнение, но технологический процесс в цеху живо напомнил покраску автомобилей. Это когда элемент в очередной раз зачищают, обезжиривают, затем наносят слой ЛКМ в специальной камере, куда вход разрешен только специалистам в соответствующей униформе. Потом – сушка под определенным светом, давлением и влажностью.
И вот перед нами склад готовой продукции. Все тщательно упаковывается и автоматически распределяется по заказам. И вскоре у кого-то из земляков или жителей «большой» России в доме появятся новые красивые двери.
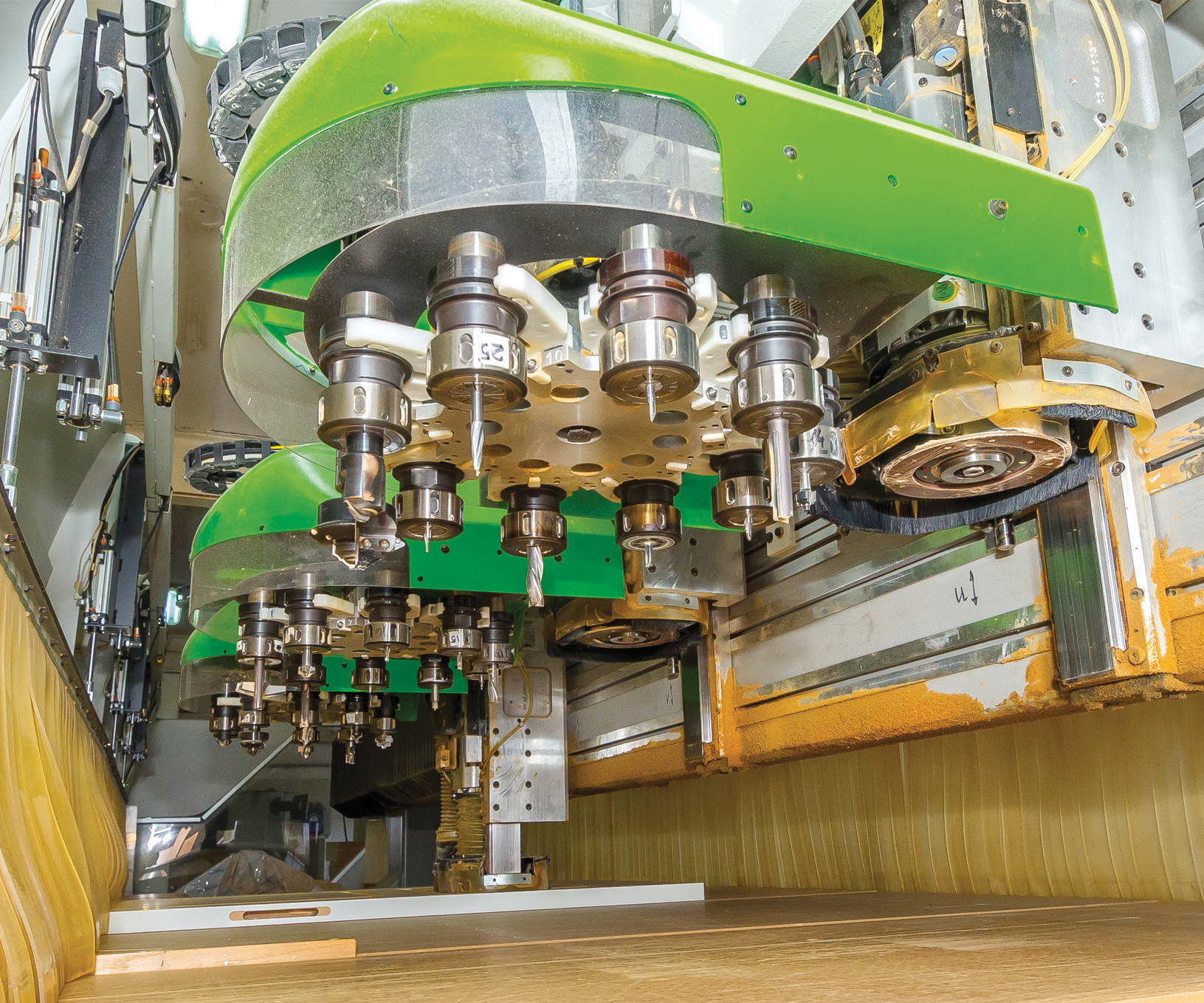
«Внутренности» фрезерного станка.
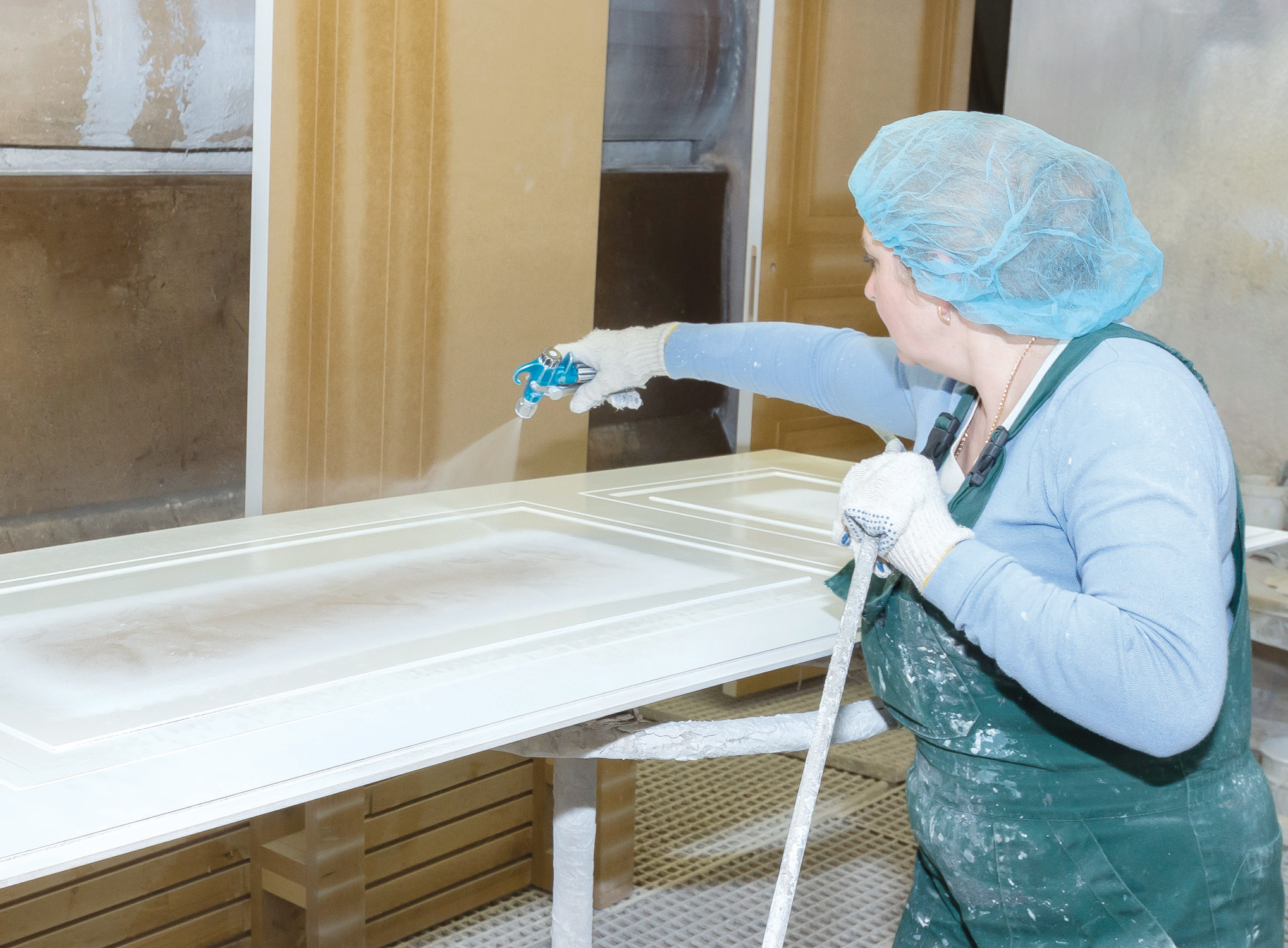
Грунтовку на полотно напыляют дважды.
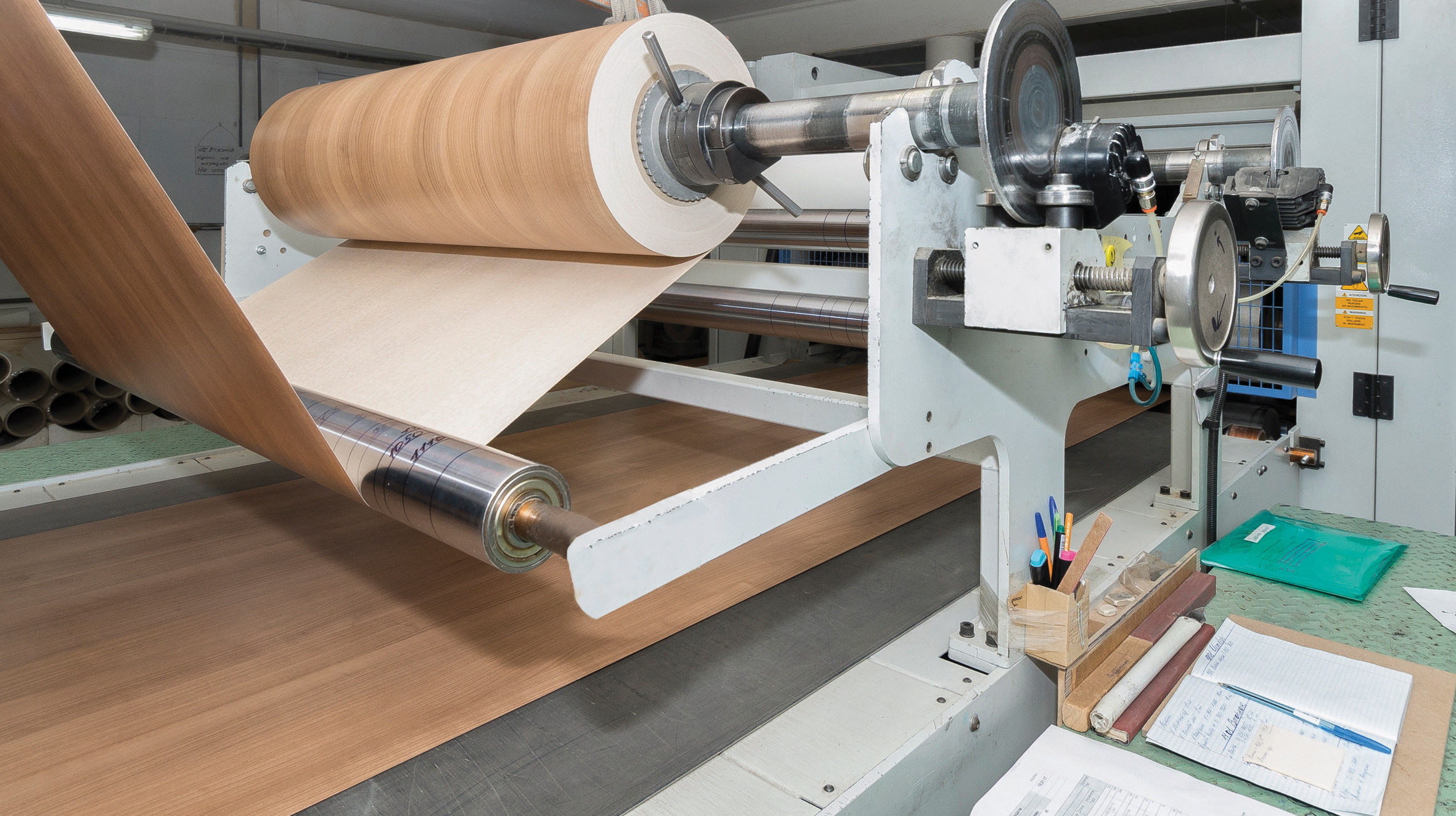
Участок кашировальной линии для облицовочного материала.
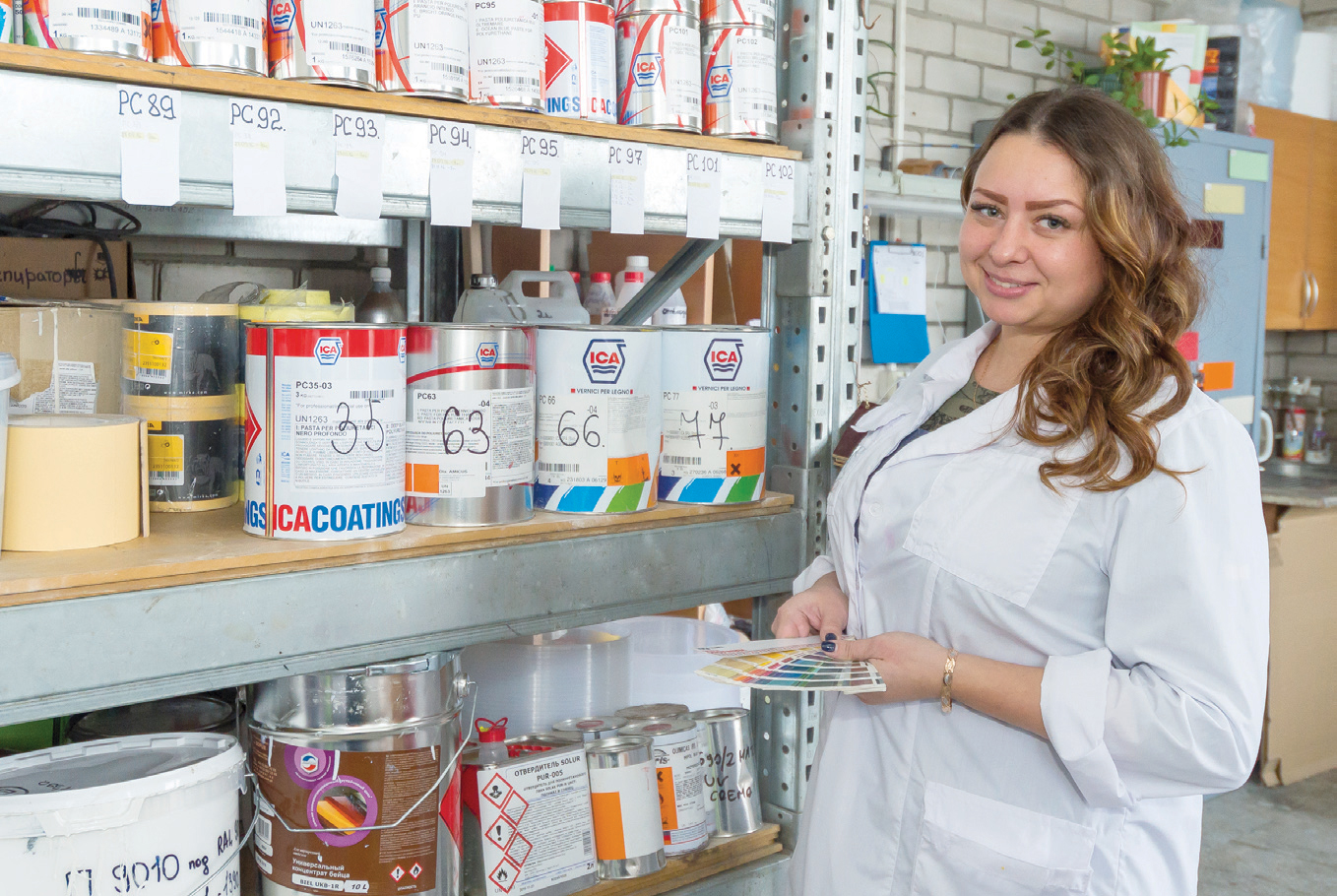
Лаборант Евгения Иванова.