Текст: Андрей Забелкин
Фото: Роман Городко
С юности помню передовицы местных газет, новостные сюжеты на телеканале «Янтарь», репортажи по радио о том, что «Завод ЖБИ-2» то перевыполнил план, то внедрил новые для Калининградской области технологии, то получил награду на ВДНХ. Однако посетить знаковое для региона предприятие удалось лишь сейчас.
– Без касок на территорию завода нельзя, – говорит нам сотрудник коммерческого отдела Денис Ханбеков. Надеваем прочные головные уборы с логотипом «Завод ЖБИ-2», и по тихим светлым коридорам Денис ведет нас куда-то вниз. Он открывает очередную дверь, и мы словно попадаем в другой мир – заводской. Шум, скрежет, лязг. На резонный вопрос, почему снаружи этого не слышно, Денис отвечает:
– Предприятие находится рядом с жилыми домами, поэтому шумоизоляции уделяется особое внимание. Кстати, не вы первые удивляетесь такому «звуковому» контрасту.
Арматурка – так любя рабочие называют цех, где готовят металлические каркасы для будущих железобетонных изделий. Здесь лабиринты из паутины всевозможной арматуры, прутов, сеток, каркасов. Впрочем, паутину здесь плетут чуть ли не в прямом смысле. Специальные «вязальные» машины создают из бухт стальной проволоки такие замысловатые конструкции, что диву даешься. На соседнем станке мужчины занимаются точечной сваркой, рядом их коллеги варят конструкции из толстой арматуры.
Как в кинотеатре
Наверное, с таким многие сталкивались: в кинозале тухнет свет, и тут – бац по ушам низкочастотным звуком. Так киношники демонстрируют возможности очередного «живого» формата Dolbi. Однако настоящий «живой» звук – в цехе панелей перекрытий ЖБИ-2. Там вибрируют станины агрегатов, в которых формы с армированием заливаются бетоном. Звук становится более мощным, когда заполненная форма прессуется сверху уплотнительной станиной.
Подстать «живому» звуку и окружающая картина: снуют люди, движутся станки, работают бетоноукладчики и краны, из репродуктора доносится: «Первый – три, пятый – два, четвертый – один...»
– Это команды, куда и кому кран сейчас будет передавать изделие или что и где следует грузить, – говорит начальник цеха Александр Мартынов. – Например, сейчас вон ту панель переместят с вибростола в пропарочную камеру.
В камере температура около +800С. Здесь панель окончательно затвердеет, затем отправится на склад.
Властелины колец
Александр Мартынов ведет нас дальше по заводу.
– А это наша новинка, – говорит Александр, показывая на ряд бетонных «беговых дорожек». – Совершенно новая для Калининграда технология производства панелей перекрытия с предварительно напряженным армированием. Здесь на стенде длиной 108 метров сначала укладываются металлические канаты. Затем специальной «удочкой» они вытягиваются в струну. Потом машина формует бетон в виде длинной плиты. Канаты, как вы уже поняли, являются арматурой, застывшей в бетоне. Когда железобетонная «дорожка» окончательно застывает (сушится она прямо на месте), фрезерная машина при помощи лазерной линейки режет ее на панели любой длины, которая зависит от желания заказчика.
Новшеством на заводе является и агрегат для производства бетонных колец. В нишу по периметру кольца автоматическая система сама укладывает влагостойкую полусухую бетонную смесь. А «властелинам колец», рабочим Михаилу и Руслану, надо только следить за процессом. Затем при помощи крана поднять цилиндр, который напоминает огромную форму для выпечки пирогов. Руслан ослабляет крепления формы, кран возвращает ее в чрево станка, а готовое кольцо диаметром два метра остается сушиться на площадке цеха.
Скрытые камеры
Наша экскурсия по цехам продолжается. В новом цеху идет заливка свай. Здесь значительно тише. Александр Мартынов поясняет, что цех запустился в этом году и позволяет заливать сваи любого сечения и длины. Мы видим, как одновременно сваенавивочная машина плетет кружева, точнее, каркасы для следующей партии свай. Часть этих свай будет забита на острове рядом со строящимся стадионом, другая станет основанием новых жилых домов.
Показывает нам Александр и универсальный стенд, с помощью которого изготавливаются лестничные марши нестандартных размеров для зданий, что проектируются по индивидуальным заказам.
Затем мы выходим на улицу, где перед нами возвышаются горы песка, щебня, гравия. Как нетрудно догадаться, это сырье для производства бетона.
– Сырье мы берем со своего карьера «Каменское», – поясняет Денис Ханбеков. – Там тоже работает самое современное оборудование и применяются передовые европейские технологии. Поэтому фракции сырья на завод поступают уже, так сказать, готовыми к употреблению.
Мы заходим на современный бетоносмесительный узел (БСУ), где на пульте управления все мигает и движется.
– Таких узлов, закупленных в Германии, у нас три, – говорит начальник бетоносмесительного цеха Сергей Тетевин.
На загрузку подъезжает очередной грузовик с вращающейся цистерной. Наполняет бетоновоз оператор Андрей Насикан. Наполняет, разумеется, не вручную, а из операторской. Перед Андреем на мониторах 18 бункеров, наполненных сырьем, химдобавками и водой с разной температурой. В зависимости от требуемой марки бетона оператор при помощи компьютера смешивает сырье, и в автобетоносмеситель поступает материал необходимого качества. За всем процессом Андрей Насикан следит при помощи видеокамер, установленных в бункерах.
Лаборатория
Только открываем дверь в заводскую лабораторию и тут же непроизвольно вздрагиваем от резкого звука – словно кирпич об асфальт разбился.
– Не пугайтесь, – успокаивает руководитель ОКП и КП Сания Байбекова. – Это мы испытываем на прочность новые образцы. Сейчас еще один под пресс пустим.
Между двух станин пресса помещается образец марки «четырехсотого» бетона. То есть он должен выдержать нагрузку в 400 кг на один квадратный сантиметр. Компьютер показывает подаваемую нагрузку: 200, 300, 400, 500… 594. И только при последнем параметре «кирпичик» разрывается на части.
– Это значит, что реальная марка данной партии – практически 600, – не без гордости говорит Сания Кашафовна. – Вот такой запас прочности мы даем для нашего бетона.
Другие образцы данной партии в это же время проверяются на водонепроницаемость и морозостойкость. Но сей процесс гораздо более длительный, поэтому мы, не дождавшись результатов тестов, отправляемся на склад готовой продукции.
Длинномер за кольцевозом
Длинные штабеля готовой продукции: панели, сваи, кольца, блоки, лестничные марши, парапеты, кабельные колодцы, сваи… Между ними – проезды для загрузки. Все они заняты спецтехникой, в которую с помощью мостовых кранов загружается продукция.
– На подъезде еще десяток машин, – останавливает нас завскладом готовой продукции Валентина Жукова. – Поэтому, ребята, извините, не могу уделить вам даже минуту времени, простой недопустим.
– В день мы отгружаем до пятисот кубов готовой продукции и около шестисот кубов бетона, – поясняет нам начальник коммерческого отдела Лариса Сурина, когда мы возвращаемся в коммерческий отдел. – Для Калининграда это неплохо, тем более в нынешнее время, непростое для застройщиков, к каждому из которых на заводе относятся с пониманием, всегда пытаясь найти обоюдовыгодное решение. И если вам показалось, что на складе все происходит хаотично, то это далеко не так. Процесс отлажен как часы. Так наш завод работал, работает и работать будет.
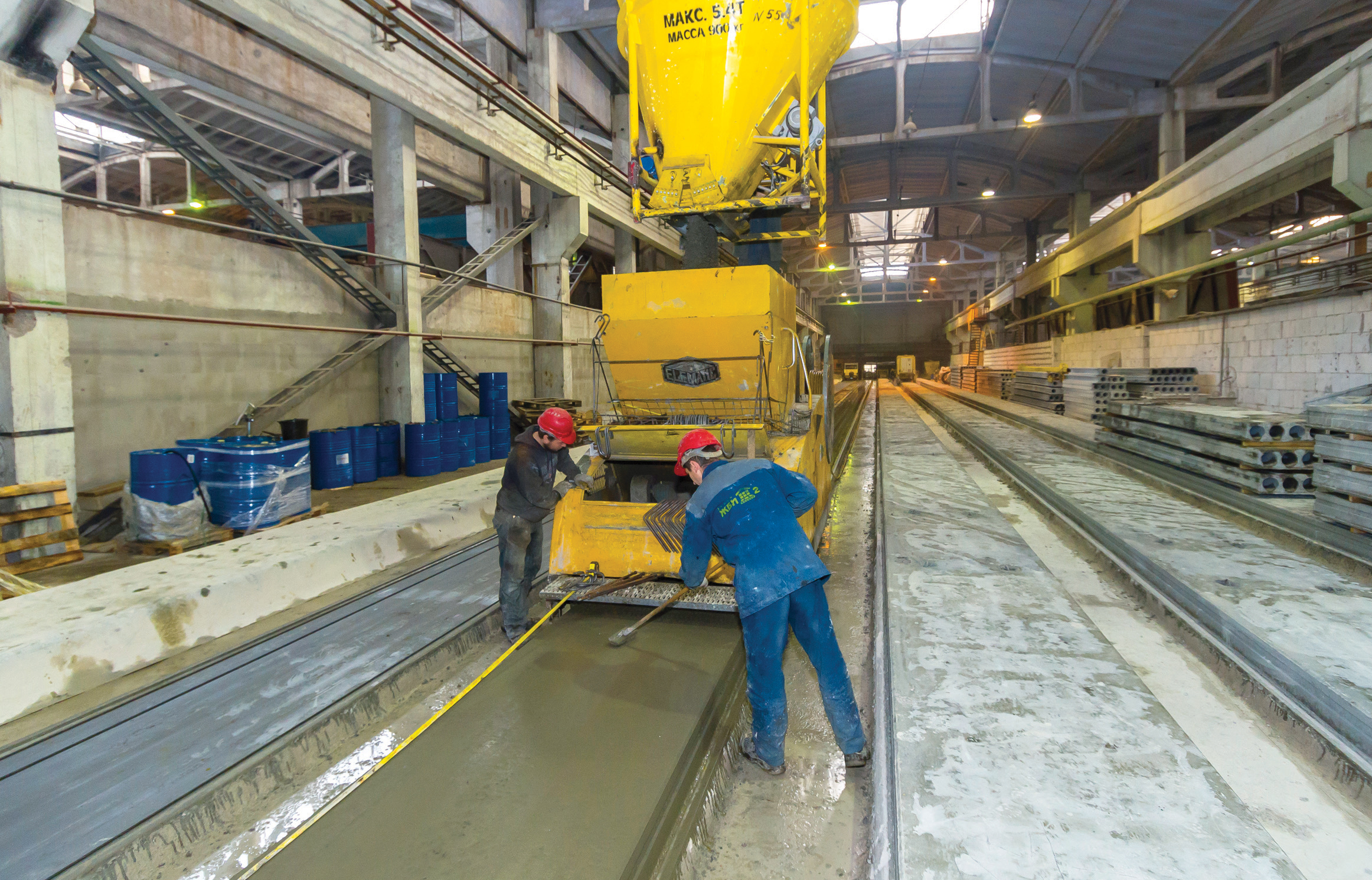
Технология с предварительным натяжным армированием.
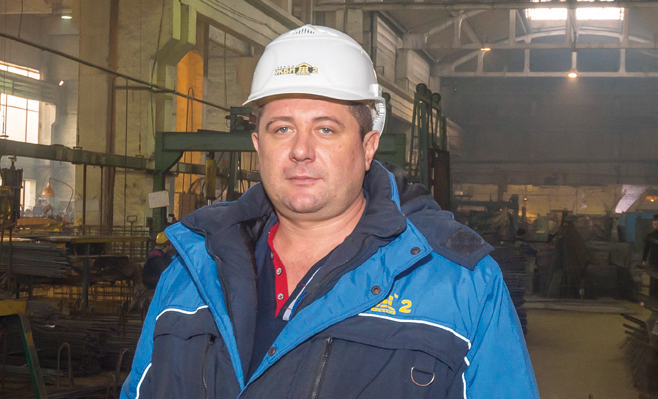
Александр Мартынов.
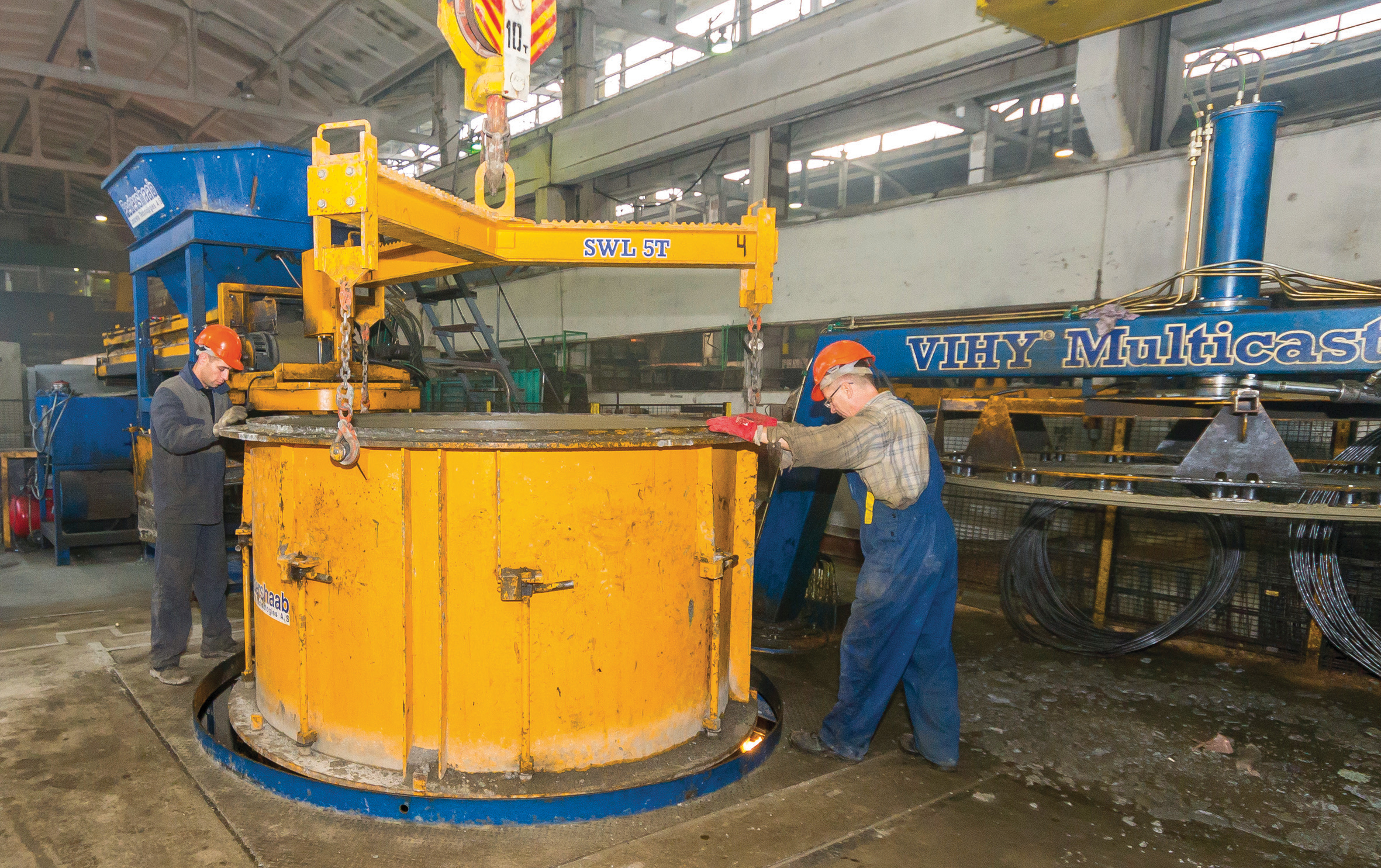
Агрегат для производства колец.
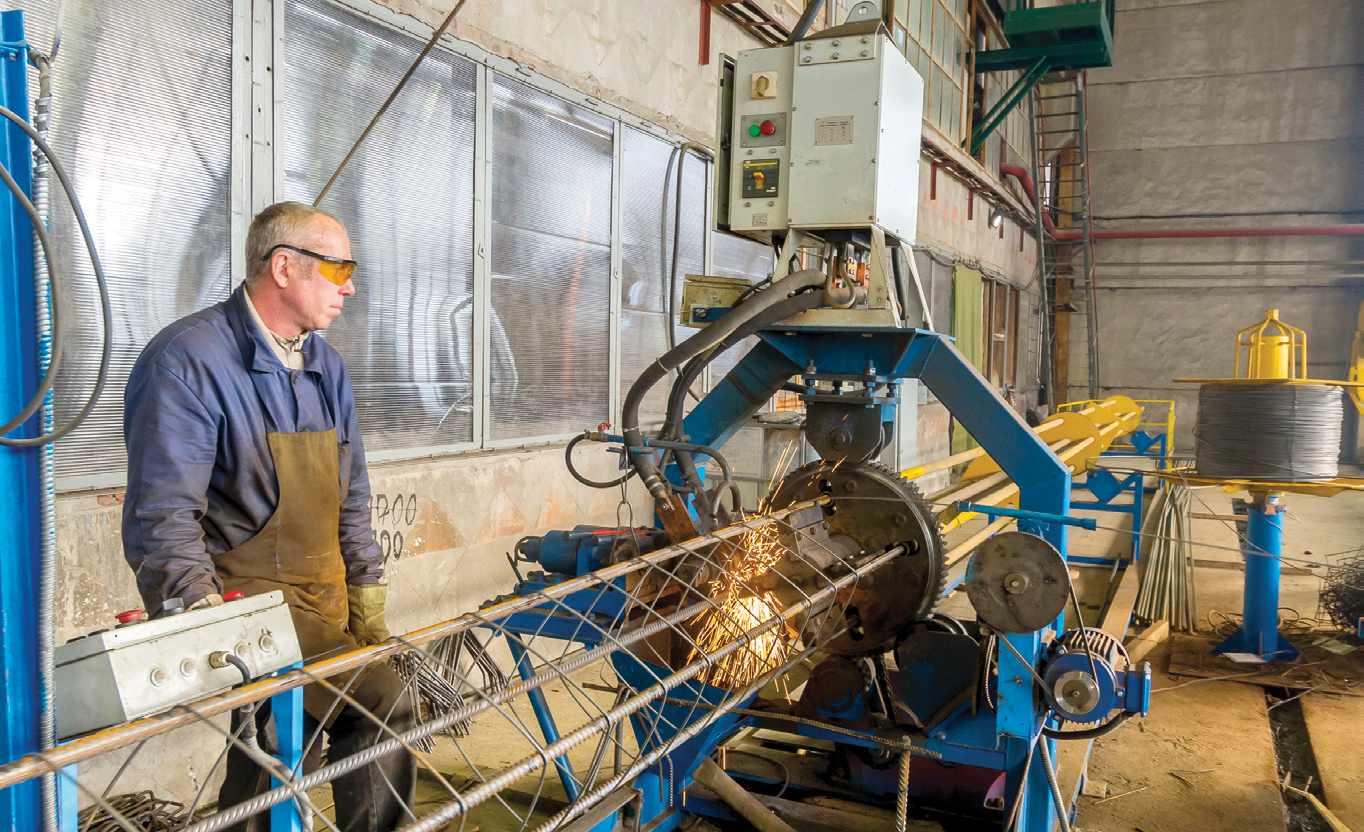
Сваенавивочная машина.
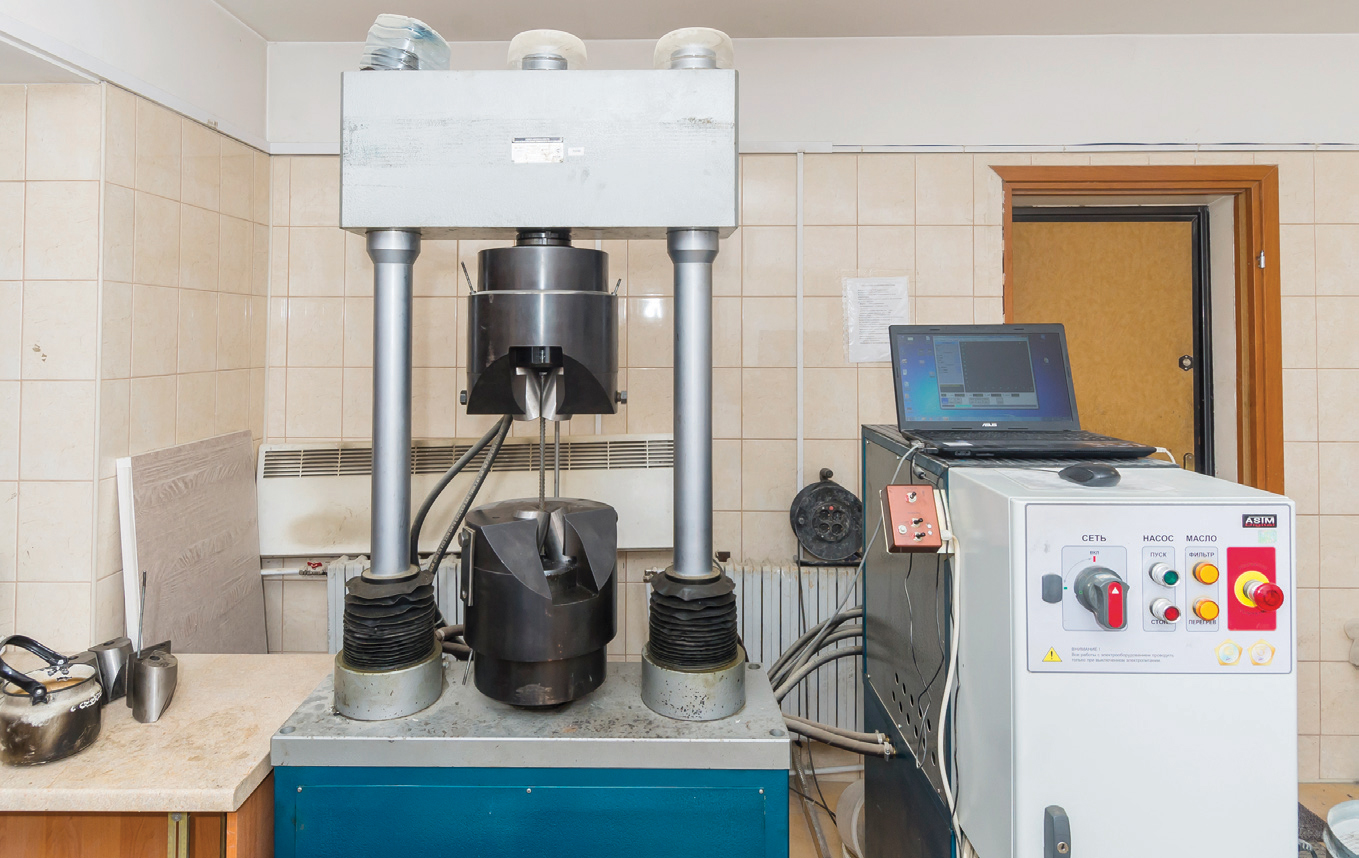
В лаборатории арматуру проверяют на разрыв.
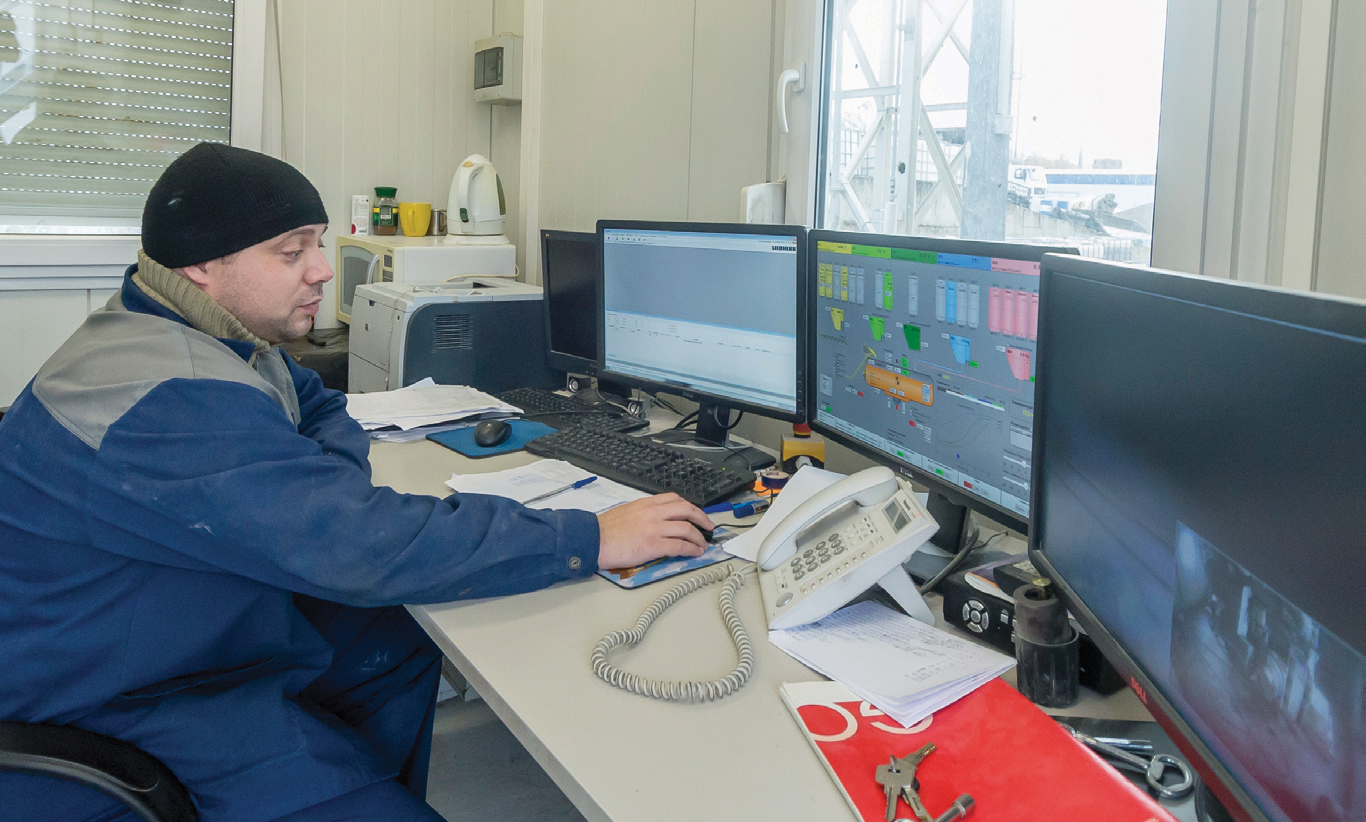
Андрей Насикан при помощи компьютера смешивает бетон.
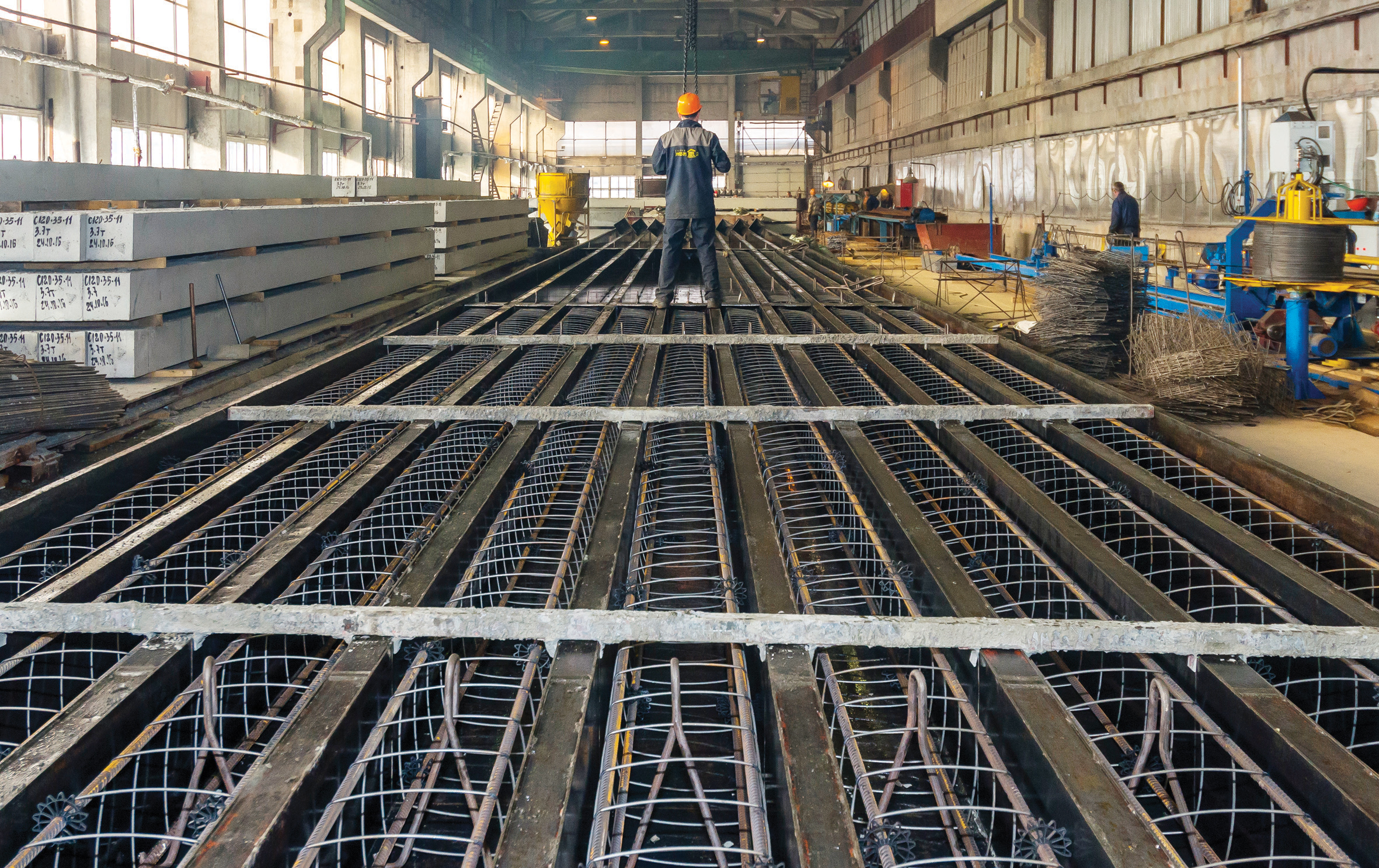
Цех заливки свай.
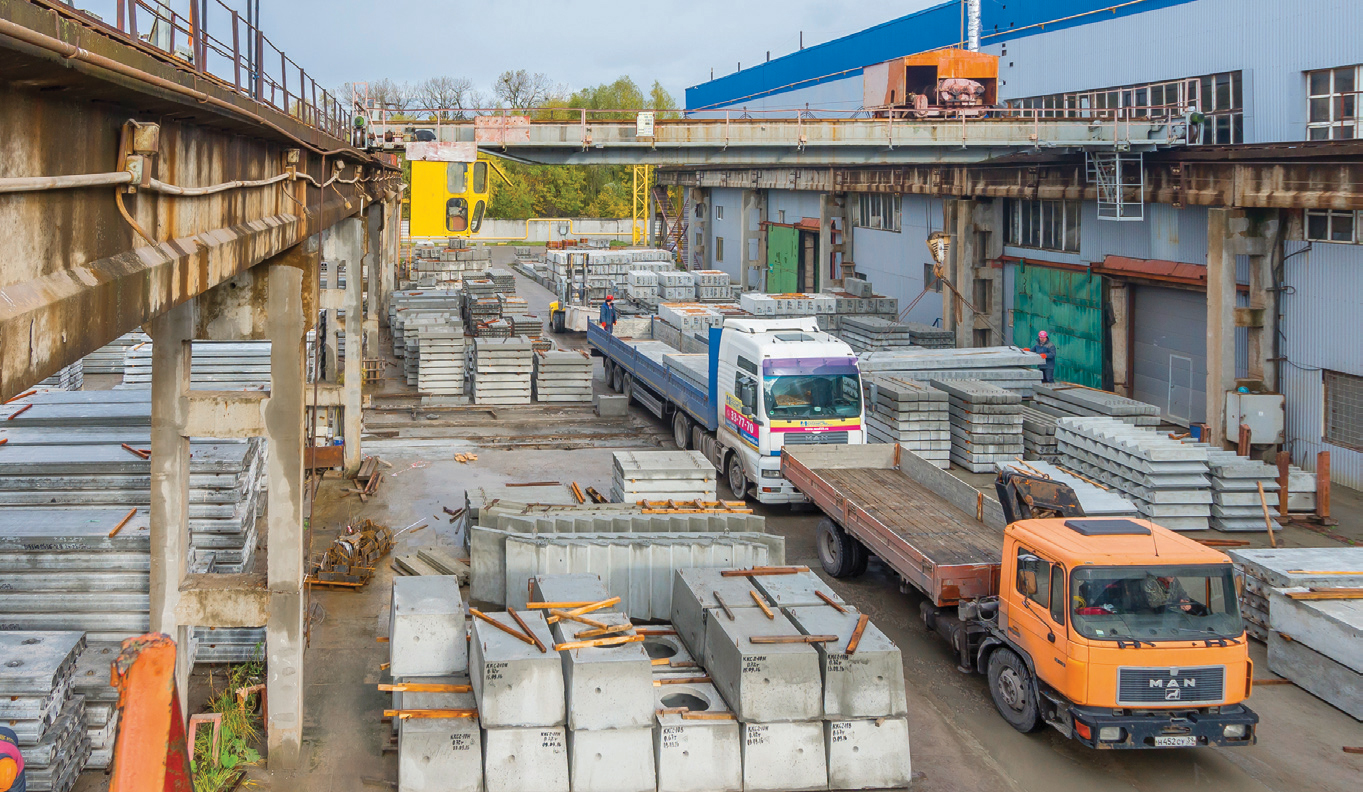
На складе идет отгрузка продукции.