Текст: Андрей Забелкин
Фото: Роман Городко, из архива компании
Репортаж с фабрики компании по производству светопрозрачных конструкций из клееного бруса сосны, лиственницы и дуба.
Почему на современных деревянных окнах нет следов от сучков? Ведь, по идее, сучки для древесины – неизбежный природный дефект. При этом на раме не видно ни одного стыка. Попробуем разобраться, как достигается такое качество материалов.
От «кругляка» до клееного бруса
На складе предприятия – штабель из заготовок, доставленных аж из Кировской области. В основном это дуб и сосна. Все они имеют радиальный распил и высушены до необходимого уровня влажности. На заготовках, разумеется, есть сучки и так называемые смоляные карманы.
Начальник цеха Валерий Двинянин поясняет:
– Дефекты удаляются. Берем, к примеру, вот эту доску, где есть такие места. И на специальном станке оптимизируем заготовку, то есть оставляем только древесину, не имеющую пороков.
Станок включается, из-под него выходят прямоугольные, разные по длине заготовки. И все они «перекочевывают» на другой станок. Точнее, это автоматизированная линия сращивания по длине. Сначала заготовки зарезаются под микрошип (это множество зубчиков на торце) с одной стороны, затем станина сама подает их под зарезку с другого края. Конвейерная лента укладывает заготовки в нужном направлении. В следующей части станка шипы проклеиваются, и заготовки намертво сращиваются друг с другом. Теперь остается ждать, когда застынет клей. И вот теперь шестиметровая клееная ламель приобретает дополнительные прочностные характеристики.
– Кстати, по качеству ламель лучше цельной древесины, в которой из-за непрерывной структуры дерева имеется внутреннее напряжение. Срощенные же заготовки менее подвержены короблению и растрескиванию. Ведь у них нет единой структуры, поэтому отсутствует и напряжение, – говорит Валерий.
Далее ламель ждет фрезерный станок, обрабатывающий ее сразу с четырех сторон, после чего она приобретает необходимую форму и размер для дальнейших преобразований в клееный оконный трехслойный брус.
То есть этот брус состоит из трех частей. Для этого доски укладываются штабелем в гидравлический пресс, где ламели под давлением склеиваются. Опять-таки ждем, пока водостойкий немецкий клей застынет. И с пресса снимается уже крепкий трехслойный брус, который прогоняется через упомянутый четырехсторонний станок.
Техническое задание
Нетрудно догадаться, что в наше время деревянные евроокна – высокотехнологичный товар.
На фабрики к каждому заказу индивидуальный подход. Руководитель производства Константин Тарабанько выдает новое техзадание, в котором указаны характеристики изделий и техническая карта.
Затем мастер на специальном станке устанавливает замысловатую фрезу.
– В Германии есть Институт деревянного окна, – поясняет Валерий Двинянин. – И там среди прочего проходят испытания различные виды окон и приспособления для их изготовления. Мы используем специальные разборные немецкие фрезы. В результате профиль, получаемый после обработки такими фрезами, соответствует последним рекомендациям Института окна в городе Розенхайме.
Включается станок, брус «встречается» с фрезой, и в итоге выходит одна из створок с замысловатым профильным узором. За ней – еще три.
Проклеиваем стыки, и рама устанавливается в «клещи» пресса. Давление по горизонтали – 50 килограммов на сантиметр. По вертикали – 60. Под таким напряжением раму выдерживают 40 минут. Однако дальнейшие манипуляции, согласно технологии, с ней можно производить лишь на следующие сутки.
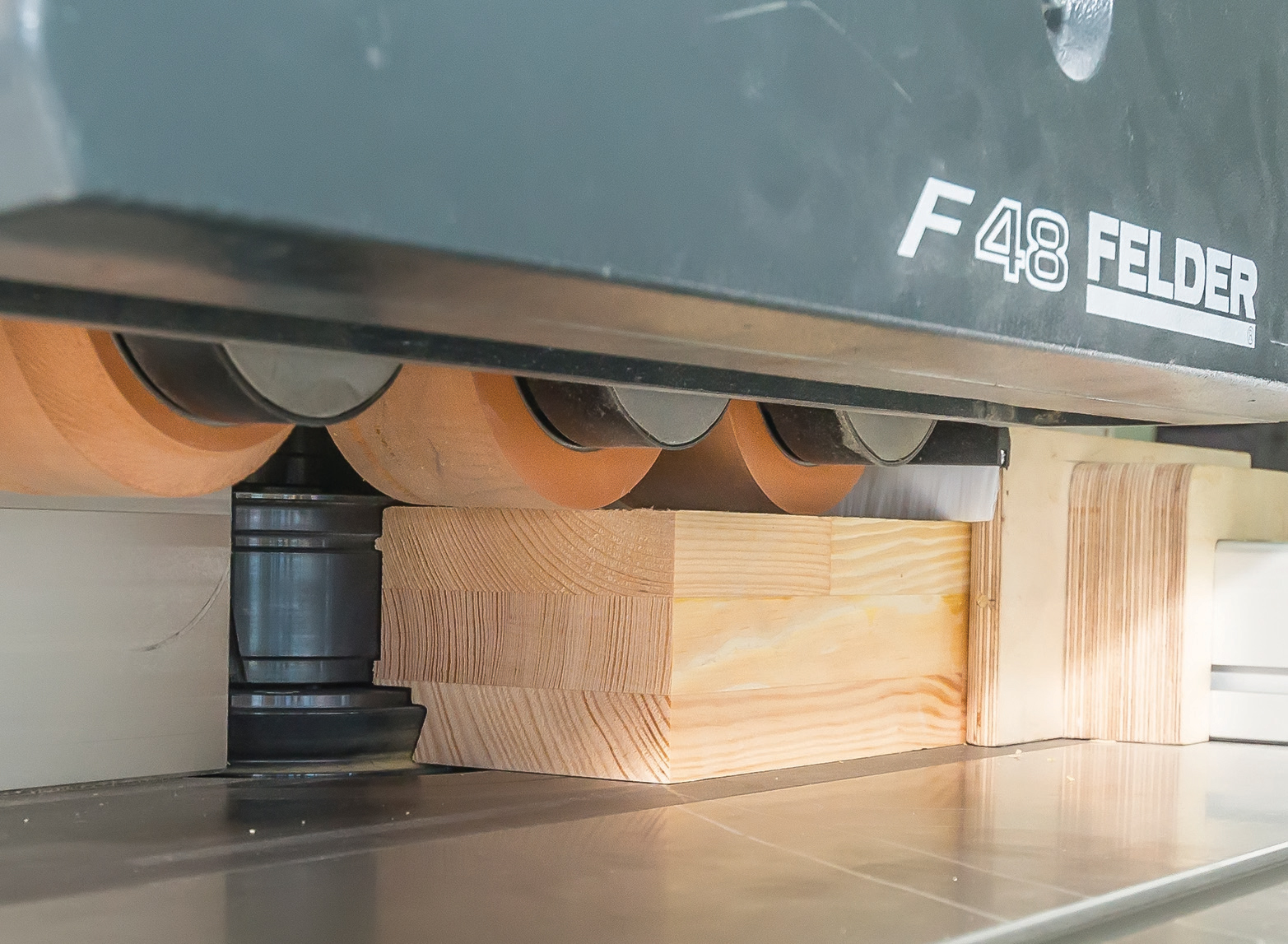
Фреза вытачивает профиль.
Водная... провокация
Грубая шлифовка открывает в дереве поры для более равномерного впитывания. Раму погружают в ванну с импрегнатом на водной основе. «Водопровокация» – так мастера называют сей процесс. И не случайно. После «водных процедур» на заготовке появляются мелкие дефекты. И если бы не провокация, то они, скорее всего, вылезли бы при следующих операциях. К слову, во время водной провокации древесина к тому же пропитывается веществами, защищающими от вредного воздействия окружающей среды.
Далее рама сушится и шлифуется. А все стыки и технологические швы обрабатываются специальным герметиком для V-образных швов. К тому же торцы промазывают прозрачной мастикой.
Теперь – очередная тонкая шлифовка на специальном станке, после чего на изделие можно наносить первый слой грунта.
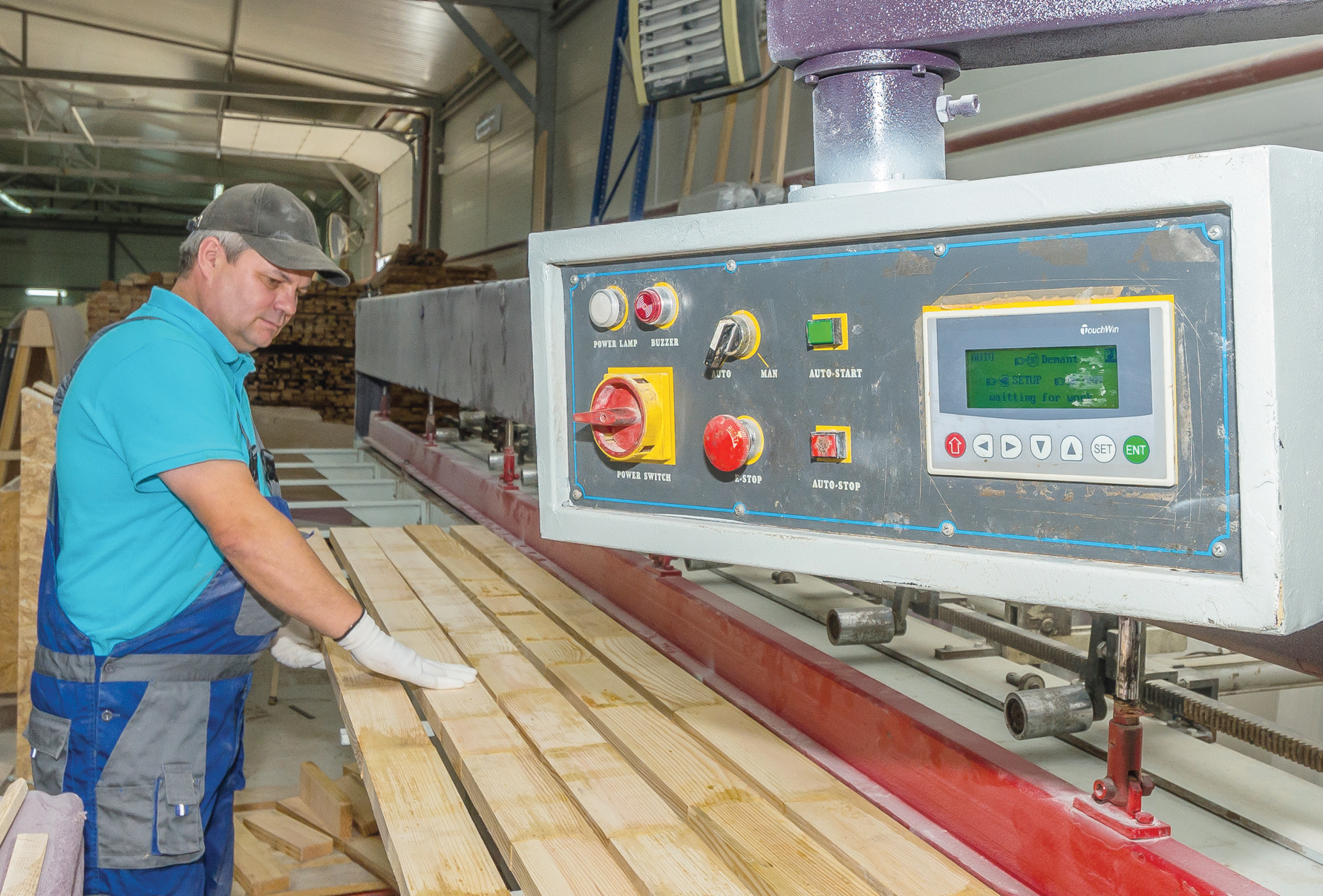
Станок по изготовлению ламелей.
Цвет без запаха
Вы когда-нибудь бывали в покрасочной камере? Будь то камеры для покраски автомобилей, мебели или окон с дверями. Химией там пахнет так, что с непривычки можно и сознание потерять. Однако в малярном цехе «Базис- Балта» – лишь запах все того же дерева.
– Мы используем лаки и краски на водной основе, – говорит маляр Евгений Елатомцев. – При этом они сверхстойкие, но позволяют дереву обладать паропропускной способностью.
Специалисты поясняют: лакокрасочный слой должен составлять 300 микрон. Это оптимальная толщина для того, чтобы окно не приходило в негодность долгие-долгие годы.
И вот рама покрашена. Осталось навесить фурнитуру и вставить стеклопакет. Мы смотрим, как специалисты ловко с этим справляются. Причем собирают они патио, то есть систему раздвижной конструкции.
Кстати, практически на каждом технологическом этапе мы имели дело с разными изделиями. Ведь деревянные евроокна, да и двери тоже, не делаются за один день. (На предприятии помимо окон производят деревянные входные двери и системы остекления типа «зимний сад» – витражное остекление).
Как сказал Валерий Двинянин, полный цикл производства одного изделия составляет в среднем 25 дней, так как даже после окраски и сборки требуется две недели, чтобы выдерживать продукцию на складе для приобретения окончательной стойкости лакокрасочного покрытия.
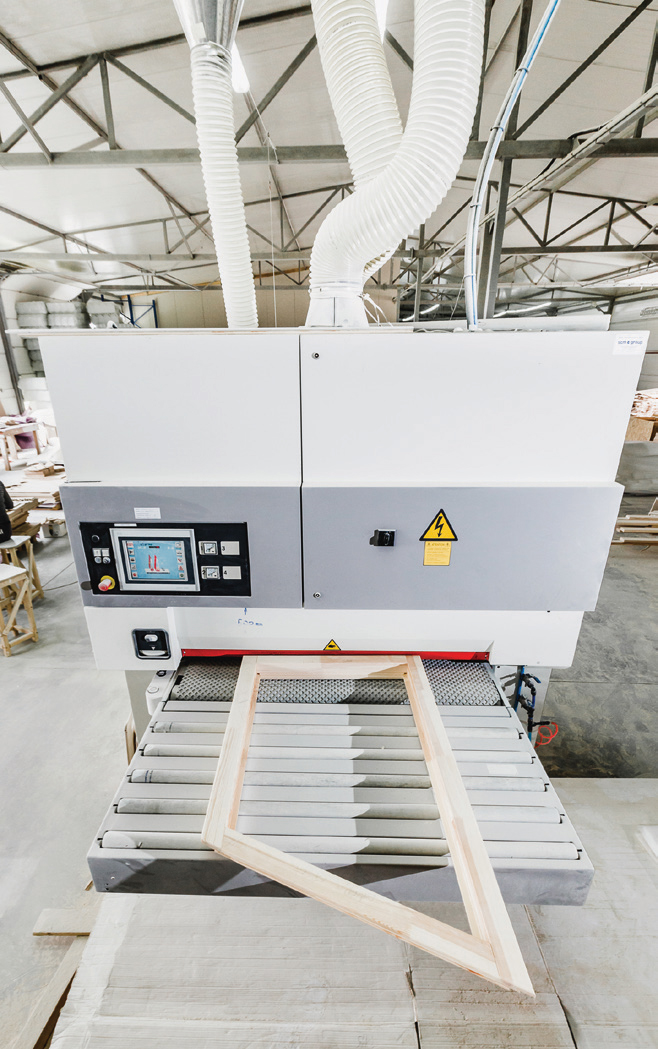
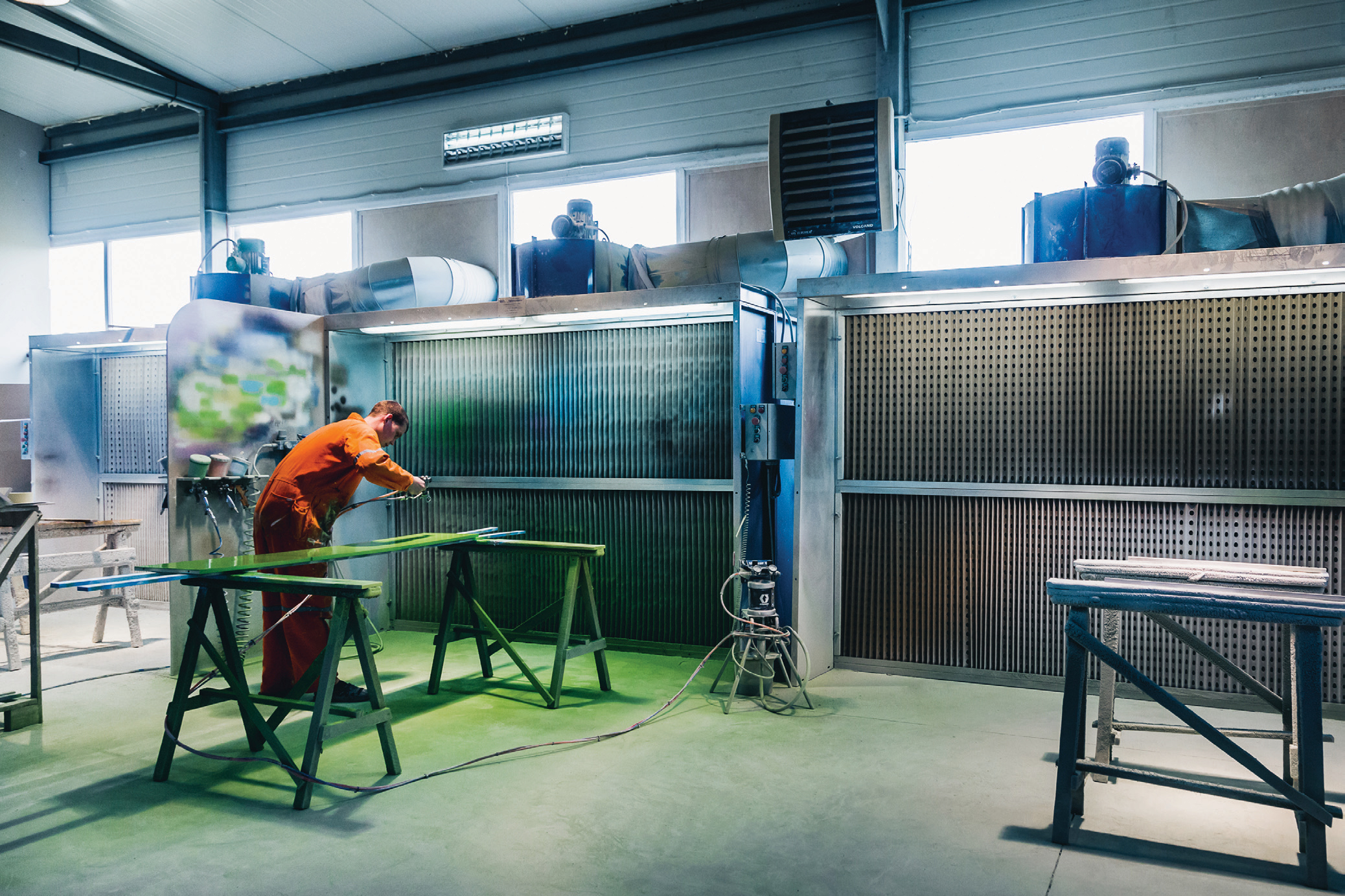
Малярный цех.