Текст: Андрей Забелкин
Фото: Роман Городко
На дворе дождь и слякоть, под ногами грязь и лужи. Но это в городе. А мы идем по чистой бетонной дороге, словно в такую погоду порядок на ней наводят с завидной регулярностью. И в доказательство этому из-за поворота появляется юркий «бобкэт», который своими щетками-насадками «полирует» проезжую часть.
А идем мы практически по лабиринту среди высоких бетонных штабелей. Точнее, газобетонных. Ведь мы на заводе «АэроБлок», где эти самые блоки и производят. И, разумеется, журналисты «СТРОЮ и ремонтирую» хотят познакомиться с «внутренней кухней» производственных процессов, как это уже происходило на многих калининградских заводах и фабриках.
Два в одном
Заходим в огромный цех. Внушительные станки, краны и прочие агрегаты гремят, стучат, скрежещут. В общем, налицо все признаки серьезного производственного процесса. Однако что-то не так… Точно! В отличие от других производств, где мы уже побывали, в помещении как-то безлюдно.
– А нам и не требуется много людей, – говорит технолог Наталья Гусева. – Все процессы автоматизированы, а за производственным циклом следят всего четыре оператора.
В операторской перед мониторами сидит Павел Кудимов. На мониторах – схемы, графики, цифры, буквенные обозначения.
– На нашем заводе происходят два производственных процесса, – продолжает Наталья Гусева. – На одной площадке мы делаем газобетонные блоки и сухие строительные смеси. В первую очередь, эти смеси идеально подходят для работы с нашими блоками. Например, газобетонные клеи для работы в летний период или, как сейчас, в зимний. Однако линейка наших смесей довольно-таки широка. Всего тридцать с лишним наименований. Это штукатурки для разных видов работ, ровнители, стяжки, растворы, затирки, шпаклевки.
По словам Натальи, процесс производства сухих смесей несложный и отлаженный до автоматизма. В зависимости от заказа или потребностей рынка в бункеры загружаются высушенный песок определенной фракции, цемент и необходимые полимерные добавки. Затем оператор задает нужную программу, которая подает в смеситель необходимое количество сырья, потом специальный робот расфасовывает готовую продукцию по мешкам. Далее мешки упаковываются в полиэтилен и складируются. Вот, в общем-то, и весь процесс.
– При этом мы производим двести тонн сухих смесей в сутки, – уточняет технолог.
Блоки
А вот газоблоков на заводе выпускается 850 «кубов» в сутки! И первое, что производит впечатление при их производстве, – мельница. Огромные жернова перемалывают… песок. При необходимости из него получается точное подобие муки. Собственно, как и мука, песок является основным ингредиентом для «выпечки» готового продукта. К нему из силосных емкостей в нужной пропорции добавляются известь, цемент, гипс, вода и то, что делает газобетонные блоки отличными от других видов строительных блоков, – алюминиевая суспензия.
Из миксеров готовая смесь заливается в шламбассейны. Впрочем, эти бассейны больше напоминают вагонетки. А при любом движении шламбассейнов по рельсам в цехе начинают реветь сирена и мигать проблесковые маячки. Мол, осторожно, состав тронулся.
При температуре 70 градусов смесь несколько часов выдерживается в камере предварительного твердения. Затем массив отправляется на резку.
Вагонетка принимает вертикальное положение, борта шламбассейна открываются, и массив остается один на один с роботами-пильщиками. Первый из них подгоняет многометровую заготовку под определенный размер – снимает с боков так называемый обратный шлам, который исчезает
в колодцах, где этот «лишний» массив будет в дальнейшем переработан.
А заготовка попадает на горизонтальный распил.
– Сегодня мы делаем блоки высотой 300 миллиметров, шириной 250 и длиной 600, – поясняет Наталья Гусева. – Поэтому струны, они же пилы, выставлены именно под этот размер.
Вот и вертикальный «пильщик» заканчивает нарезку. Теперь нарезанные блоки должны «созреть». Так, операторы называют изначальный массив «зеленым сырцом». А когда он уже готов для финальной стадии превращения в газобетон – «белым».
Финальная стадия – это погружение сформированного «железнодорожного» состава с белым сырцом в автоклавы. Не будет преувеличением сказать, что массив там превращается в столь популярный строительный материал – газобетонные блоки. Ведь под давлением в 14 атмосфер в течение 12 часов происходит химическая реакция, преображающая алюминиевую суспензию в природный минерал – тоберморит. Он-то и придает блоку уникальные качества.
После выхода из автоклава все блоки подаются на упаковку, где каждый из них осматривается работниками ОТК. Затем блоки укладываются в два штабеля. Но чтобы они прилегали максимально плотно, блоки подаются на… «ухошлепку».
– Так этот станок не мы назвали, а наши немецкие партнеры, – улыбается Наталья.
А что, похоже. Станок словно двумя огромными ладонями шлепает по штабелю, который тут же упаковывается и отправляется на склад. Затем – на калининградские стройки.
850 «кубов» газобетонных блоков завод выпускает за смену.
200 тонн сухих смесей «АэроБлок» производит за сутки.
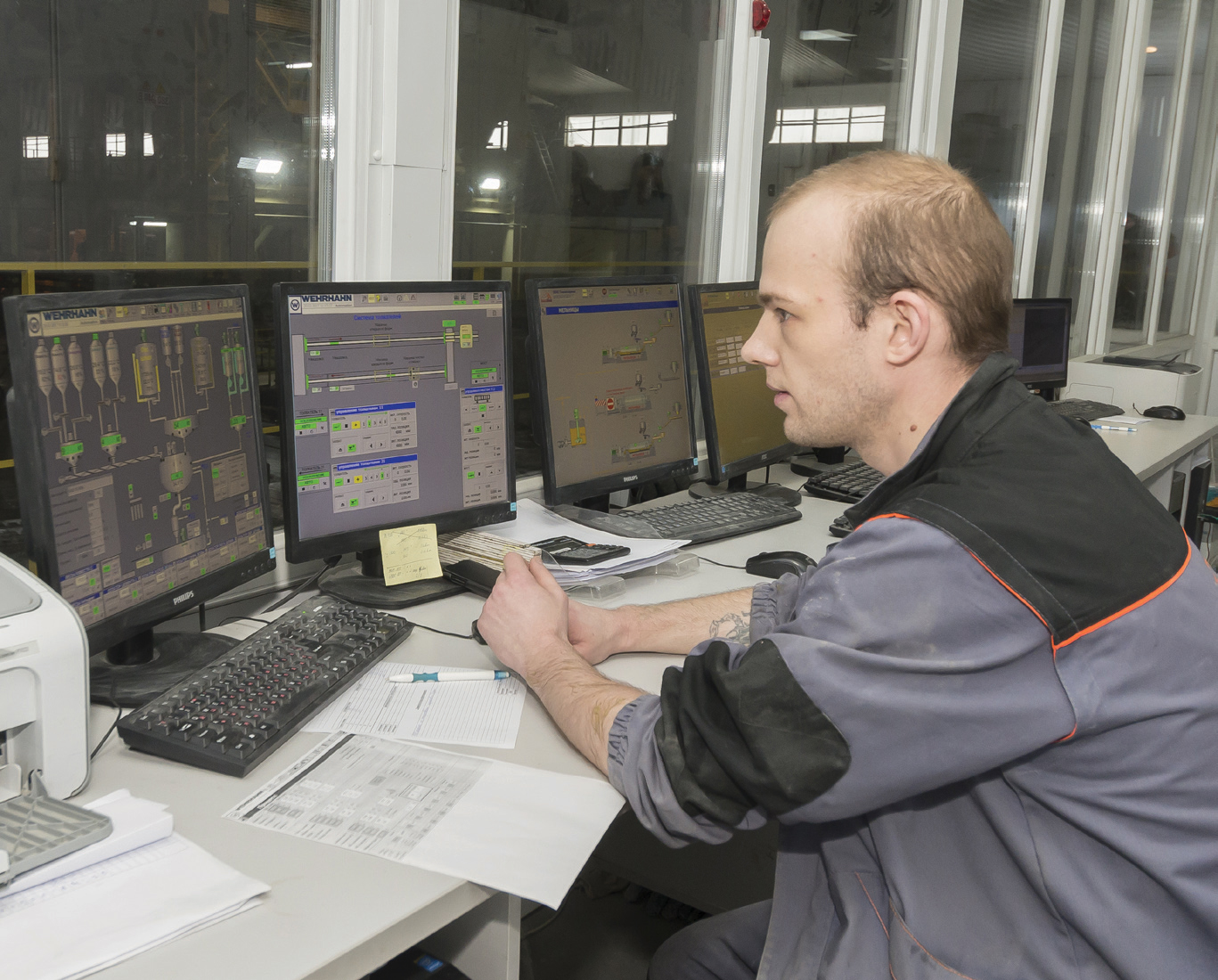
Оператор Павел Кудимов.
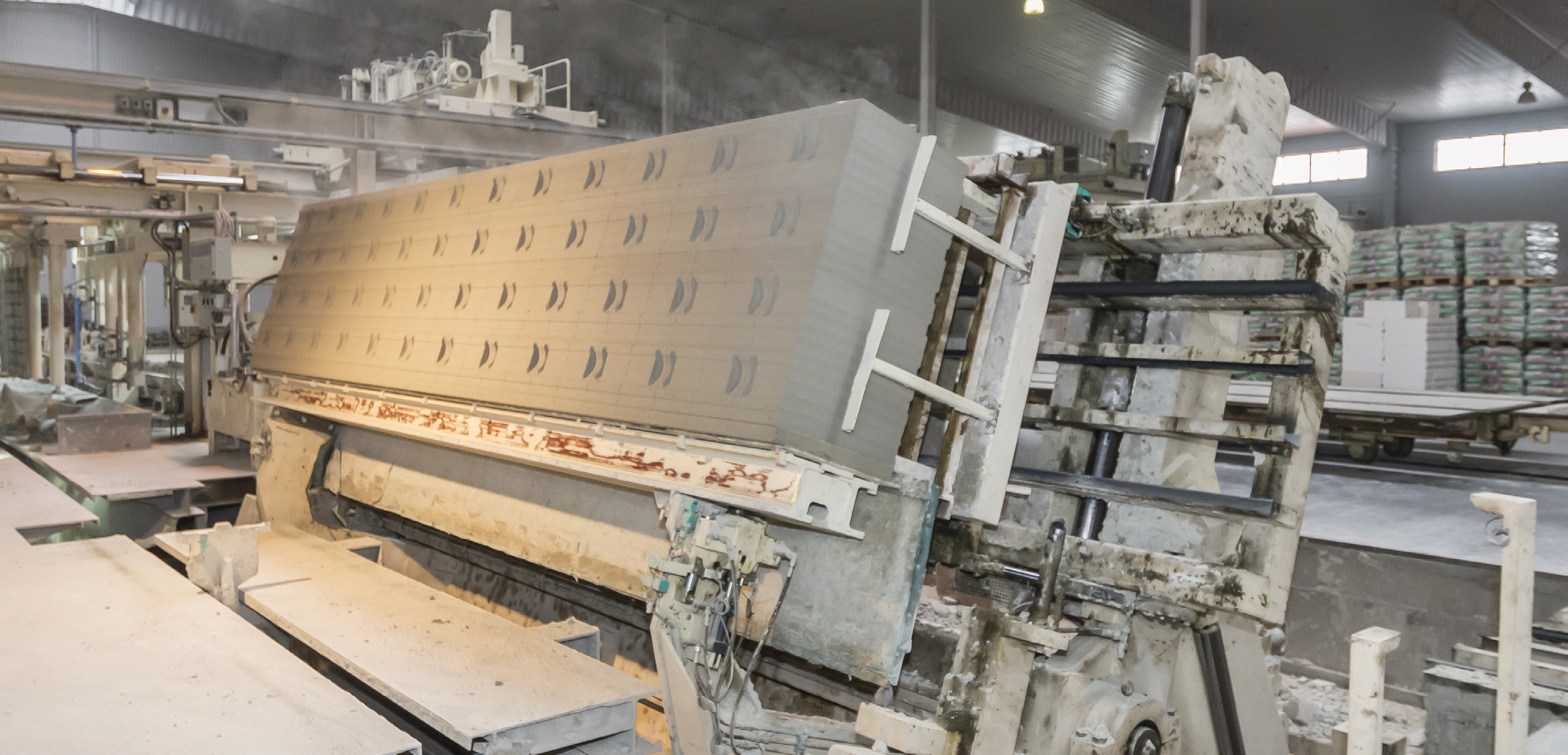
Массив на все операции подается автоматически.
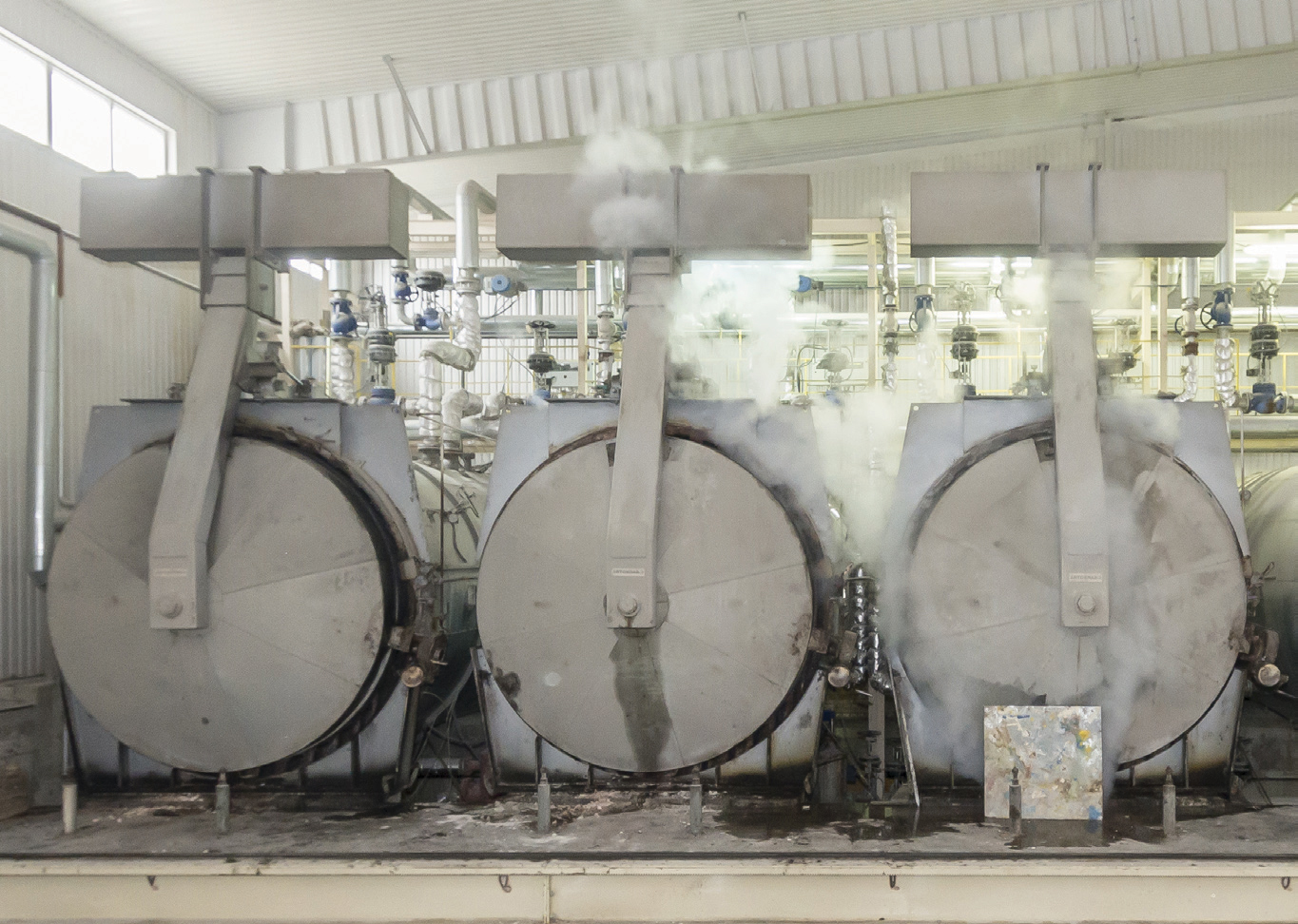
Давление в автоклаве – 14 атмосфер.
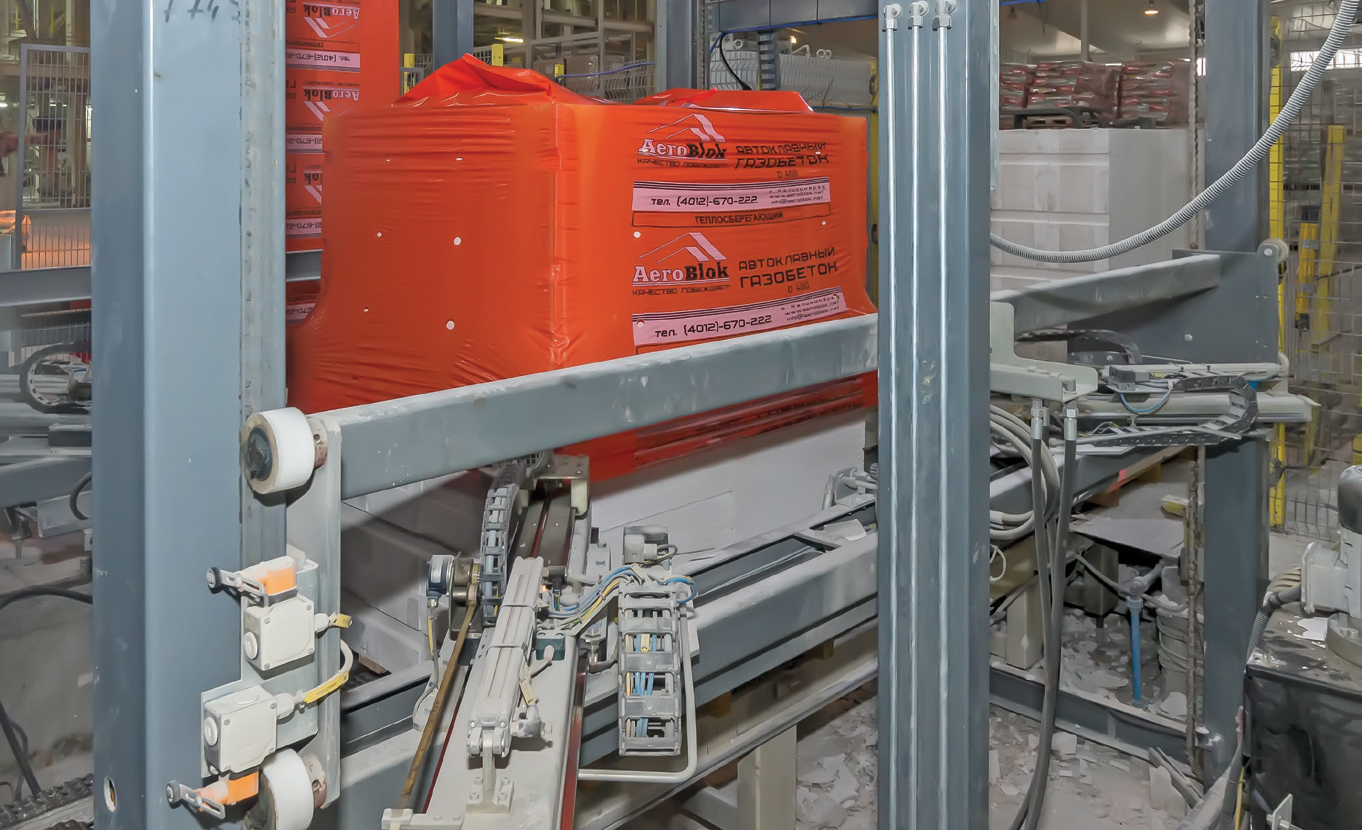
Производственный процесс заканчивается упаковкой блоков.