Текст: Андрей Забелкин
Фото: Роман Городко
Цельные стекла такого размера автор этих строк не встречал еще ни разу – 6x3,2 м, то есть 19,2 кв. м! И их здесь в специальных штабелях – сотни!
– Как такое стекло вообще можно доставить и разгрузить? – спрашиваю начальника производства завода «Пластикат-Сервис» Алексея Михеева.
– Стекло такого формата называется «Джамбо», – поясняет Михеев. – И привозят его специальные «джамбовозы». Днище у такой машины – самовыездная тележка. Этот тельфер и доставляет стекло на склад. А дальнейший процесс вы сейчас сами увидите.
Нарезал – помой
К стоящему штабелю подъезжает роботизированный станок австрийской фирмы Lisec, от него вертикально поднимается станина, которая десятками присосок прижимает к себе стекло, затем аккуратно опускает на станок. При этом стекло вибрирует, словно это лист прозрачной пластмассы. Но трескаться оно не собирается и в горизонтальном положении «доезжает» до стола раскроя.
На мониторе перед оператором Вячеславом Рыбиным лист уже раскроен. Причем каждый фрагмент имеет свою нумерацию: D-23, С-19 и так далее. Пустот на мониторе практически нет, если не считать парочки тонких прямоугольников. Скоростной режущий мост приступает к нарезке.
– Мы долго подбирали алмазные стеклорезы, ведь далеко не все они режут идеально, – говорит Алексей Михеев. – Но в конечном итоге нашли. А чтобы окончательно избежать брака, на стеклорез подается тончайшая струйка специального масла.
– Но масло же остается на стекле, – уточняю я.
Алексей улыбается: мол, не переживайте, сейчас сами все увидите.
Парочка рабочих лихо надламывает лист по срезам и сортирует стекла по тележкам в специальные ячейки. Для этого-то и нужна нумерация. Потом стекла в определенном порядке подаются в моюще-сушильную камеру.
– В камере мягкие щетки убирают со стекла все примеси, – продолжает Алексей Михеев. – А моется стекло водой, которая после прохождения системы фильтров становится чище, чем вода для производства водки. Не верите? Но такова технология, и мы ее соблюдаем.
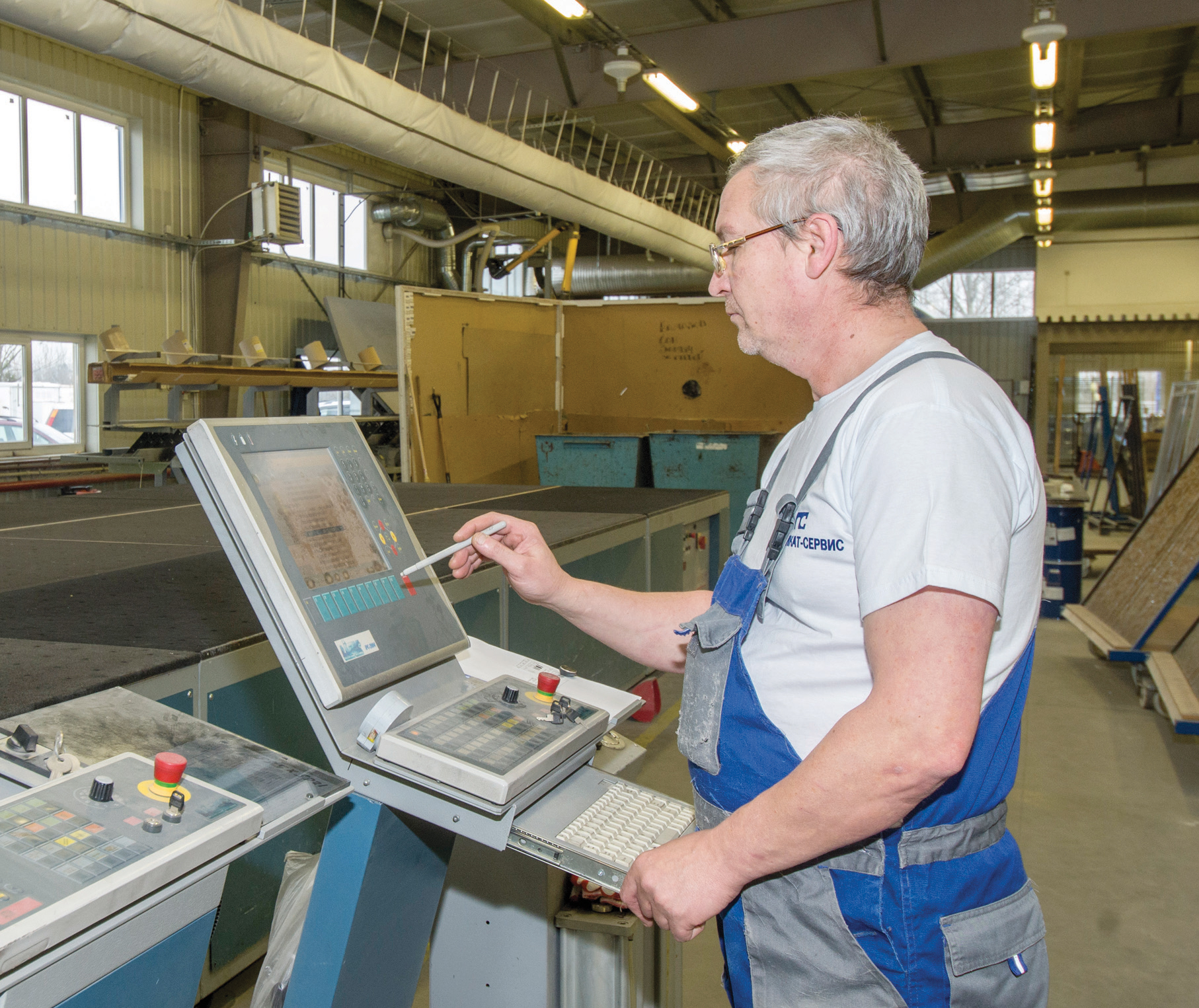
Оператор Вячеслав Рыбин.
Соблюдай дистанцию
Параллельно с нарезкой и помывкой стекла идет процесс изготовления дистанционных рамок для стеклопакетов. А дистанционными их назвали за то, что они выдерживают зазор между стеклами.
Рамки гнет специальный станок. Над ним на мониторе оператор Петр Чумаков видит те же D-23, С-19... То есть гнет он рамки под свежепомытые и высушенные стекла.
– Кстати, традиционно при изготовлении рамок в Калининградской области используются угловые соединители, – говорит Михеев. – Но как раз они могут стать причиной разгерметизации пакета. Мы же рамку гнем, что практически на 100% снижает риск разгерметизации. А единственный стык на рамке заделываем очень
тщательно. Также рамка заполняется абсорбентом, который будет забирать лишнюю влагу.
Затем в рамку вставляются стекла, и пакет подается в камеру газонаполнения, которую рабочие прозвали «Змей Горыныч». Здесь пространство между стеклами заполняется аргоном. После этого по периметру рамки автомат наносит двухкомпонентный герметик.
– Только не вляпайтесь в нанесенный герметик, – предупреждает нас Михеев. – Он ничем не отмывается. Мне в свое время пришлось не одну пару брюк выкинуть.
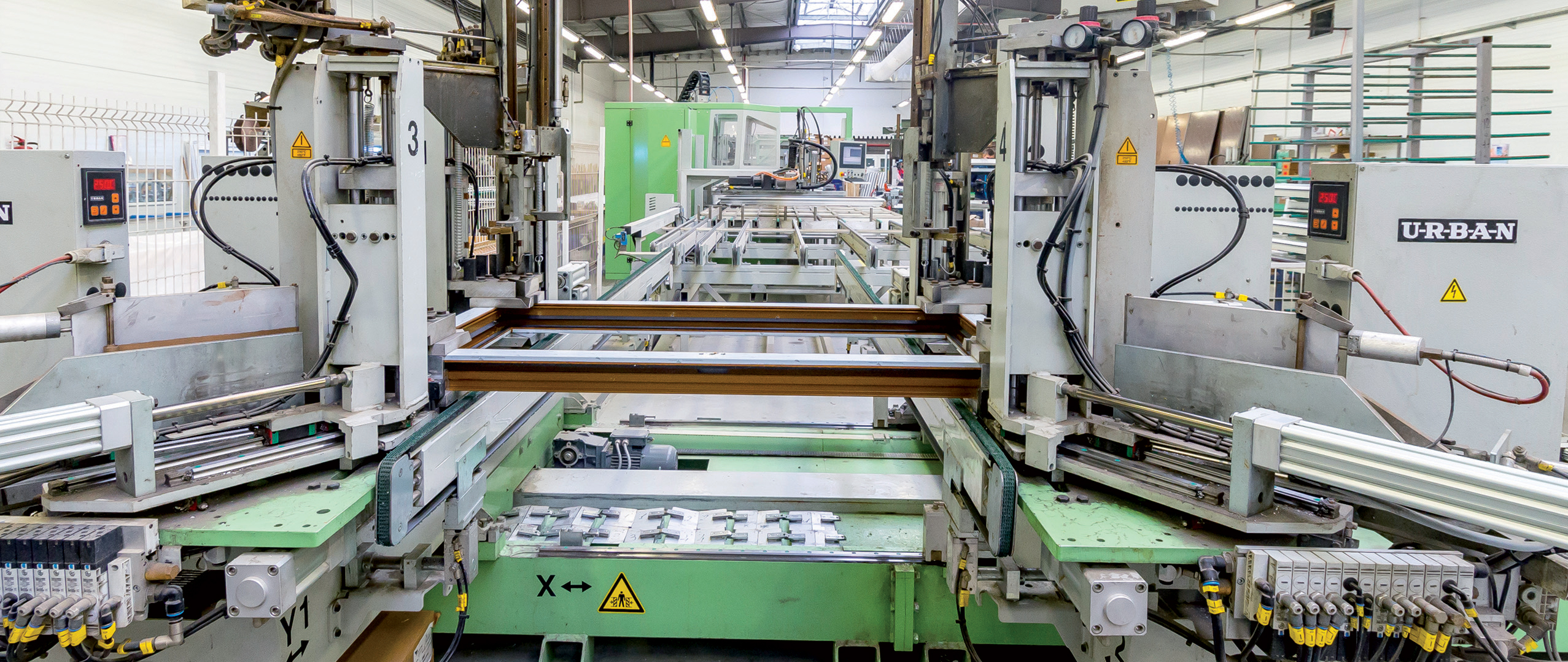
Линия четырехголовочной сварки.
Вид в профиль
Оберегая свои штаны, идем в цех ПВХ. Здесь изготовление рам, створок, дверей тоже синхронизировано с теми изделиями, которые в данный момент собираются на «стеклопакетном» участке. В частности, станок раскроя профиля способен нарезать сразу 12 заготовок под разные заказы.
– Это еще одна наша гордость, – продолжает рассказ Алексей Михеев. – Подобных станков компании SCHIRMER в Калининградской области больше нет. Сам профиль КВЕ поставляет тоже немецкая компания. Это самый надежный и удобный в работе профиль. К тому же он экологичен и более долговечен.
Далее нарезанные заготовки попадают на станок технологических отверстий. И тут, по словам Михеева, заводу есть чем гордиться. Так, обычно на подобные станки подается одна заготовка. Однако руководство «Пластикат-Сервиса» попросило поставщиков оборудования спроектировать станок таким образом, чтобы отверстия делались синхронно сразу на двух «зеркальных» профилях. Тем самым удается избежать даже малейшего расхождения отверстий в двух параллельных створках.
Далее детали армируются – внутрь пластикового профиля вставляется металл и намертво закрепляется. Ведь, как ни крути, пластик от перепада температур расширяется или сужается, а так металл не дает ему «гулять».
Немаловажный этап – склейка профиля.
– У нас используется так называемая четырехголовочная сварка, – поясняет бригадир Эдуард Юркшайтис. – То есть на станке склеиваются сразу четыре угла, что позволяет получить створку или раму идеальной прямоугольной формы. Например, кустари в гаражах, которых в Калининграде немало, клеят каждый угол по отдельности, и перекосы в таких случаях неизбежны. А народ потом удивляется, почему окно в квартире так плохо открывается.
Затем углы «идеальных прямоугольников» зачищаються, а створки опять-таки на специальных станках обвязывают фурнитурой. Один из рабочих на этом участке – Николай Горбачев.
– Здесь все продумано до мелочей. С каждой заготовкой мне поступает информация, какую именно фурнитуру я должен навесить: антивзлом, комфорт, престиж, селект… Это очень удобно. Как в армии! – смеется Николай. – Все по ранжиру. Я недавно срочную отслужил и очень доволен, что попал именно сюда. Работа хорошая, в теплом цеху, да и платят прилично.
Дальше идет участок сборки готовой продукции, где навешиваются петли. А вот и знакомые нам стеклопакеты! Остается их только вставить и заштапить. Говоря проще, закрепить пакет в раме пластиковым штапиком.
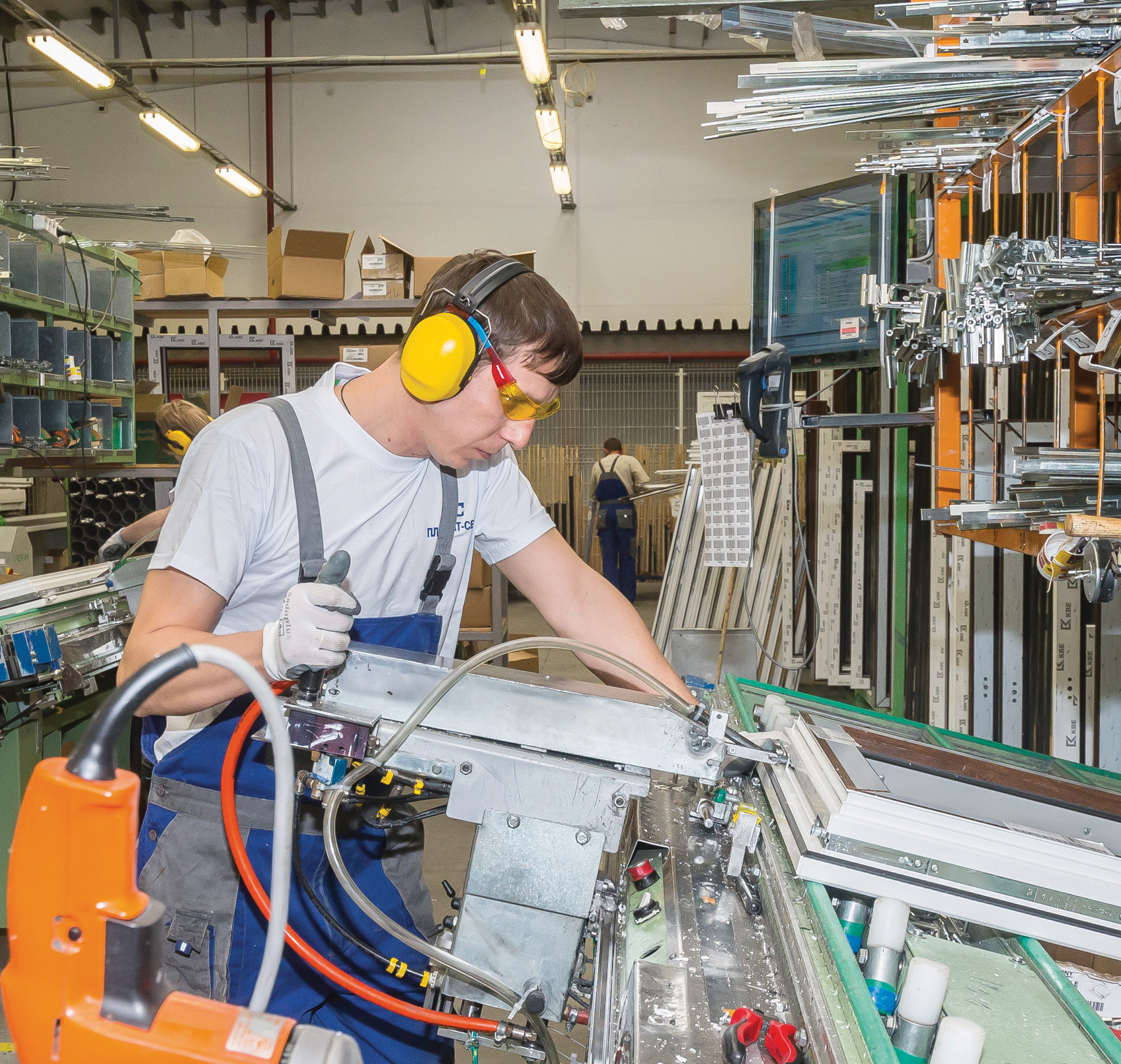
Обвязка фурнитуры на специальном станке.
Учет и контроль
Участок ОТК. Инженер Надежда Анохина тщательно осматривает каждое стекло на предмет сколов и царапин, открывает и закрывает все створки, чтобы они ходили как по маслу, электронным штангенциркулем проверяет плотность прилегания деталей.
– Но это не вся проверка, – поясняет Надежда. – Предварительно в лаборатории мы проверяем партию на специальном оборудовании.
Так и есть. В лаборатории Надежда Анохина демонстрирует нам одну из основных проверок – надежности сварного шва. Так, для стандартного окна угол должен в течение трех минут выдержать давление 188 кг/кв. см. Подтверждаем: выдерживает.
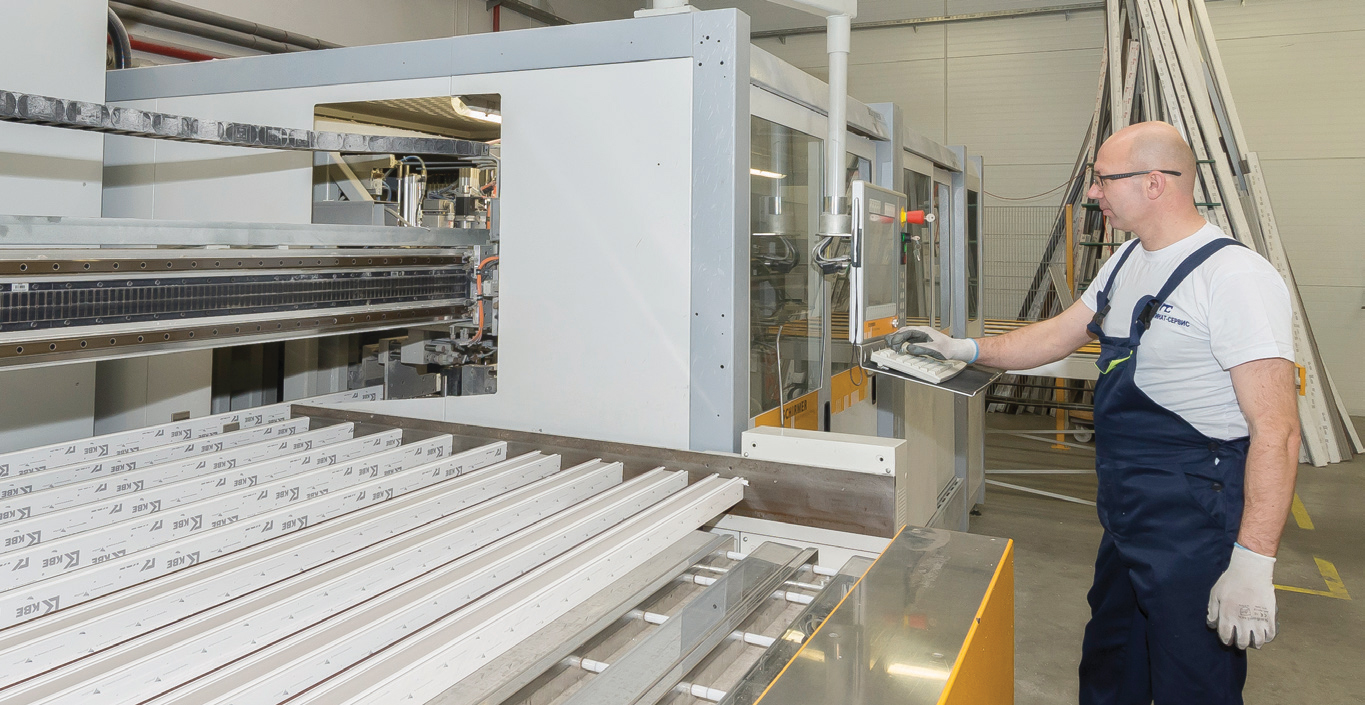
Нарезка профиля на станке SCHIRMER.
Эксклюзивные вещи
Пока мы совершаем экскурсию по заводу, к нам присоединяется генеральный директор «Пластикат-Сервиса» Евгений Ермолаев. С ним мы заходим в цех нестандартной продукции. Тут делают эксклюзивные вещи: большие витражи, изогнутые и рельефные рамы, массивные раздвижные двери и тому подобное.
– Здесь у нас трудятся мастера, которые работают на предприятии с первых дней, – говорит Евгений Николаевич. – А работаем мы с 1998 года. За долгие годы они так отшлифовали свое мастерство, что могут исполнить заказ любой сложности. И вот что, на мой взгляд, немаловажно. До многих вещей мы доходили путем проб и ошибок, а не покупали сразу готовую технологическую линию. Наша технология лучше, потому что мы доводили ее до ума сами, своими идеями и руками. Одних только рацпредложений наших смекалистых умельцев внедрили десятки! Поэтому сроки исполнения заказа у нас самые короткие. Поступил заказ – и он тут же распределяется на все линии и участки. В такой синхронизированной работе мы и получаем оптимальный продукт в минимальные сроки. Это разве не лучший результат для предприятия?
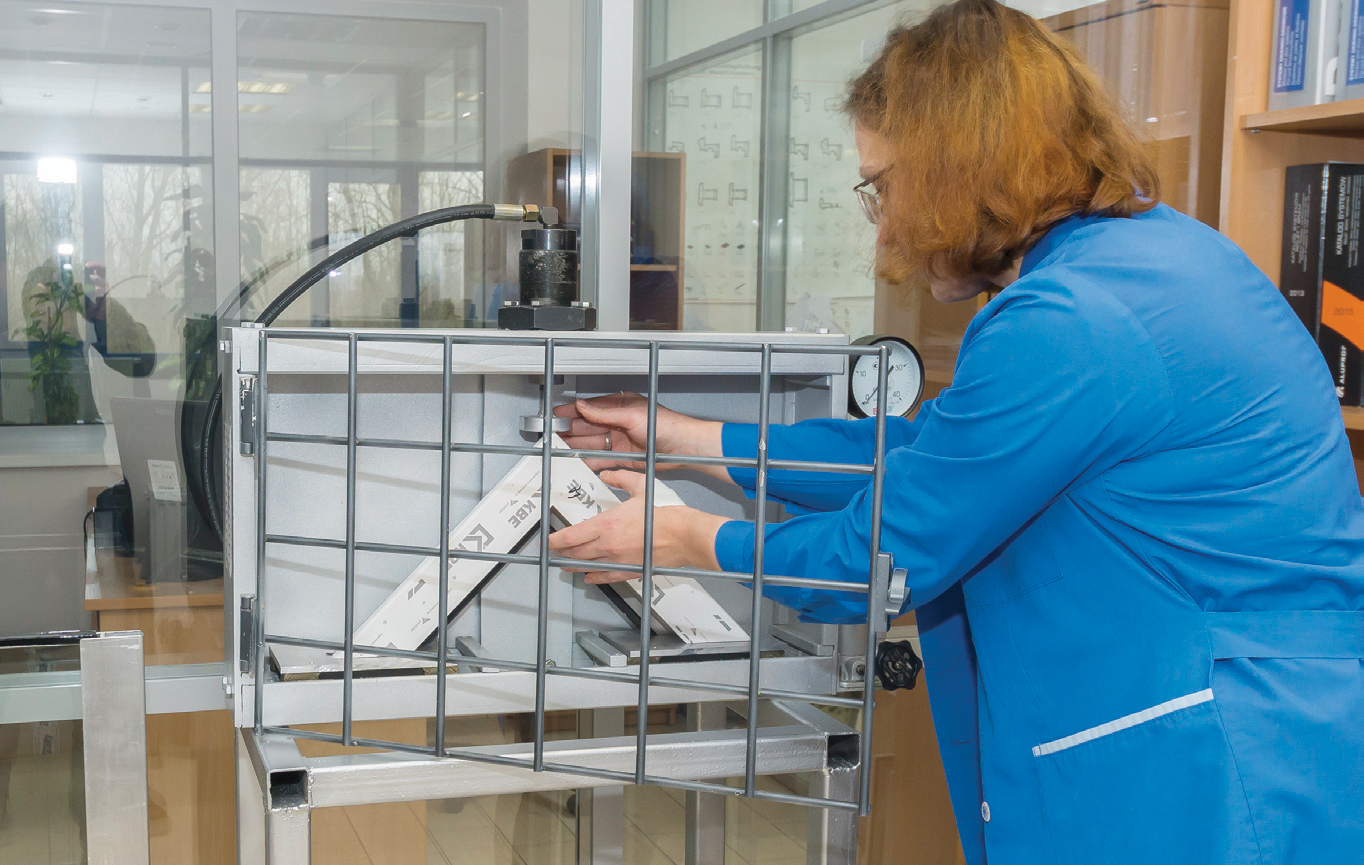
Инженер ОТК Надежда Анохина.
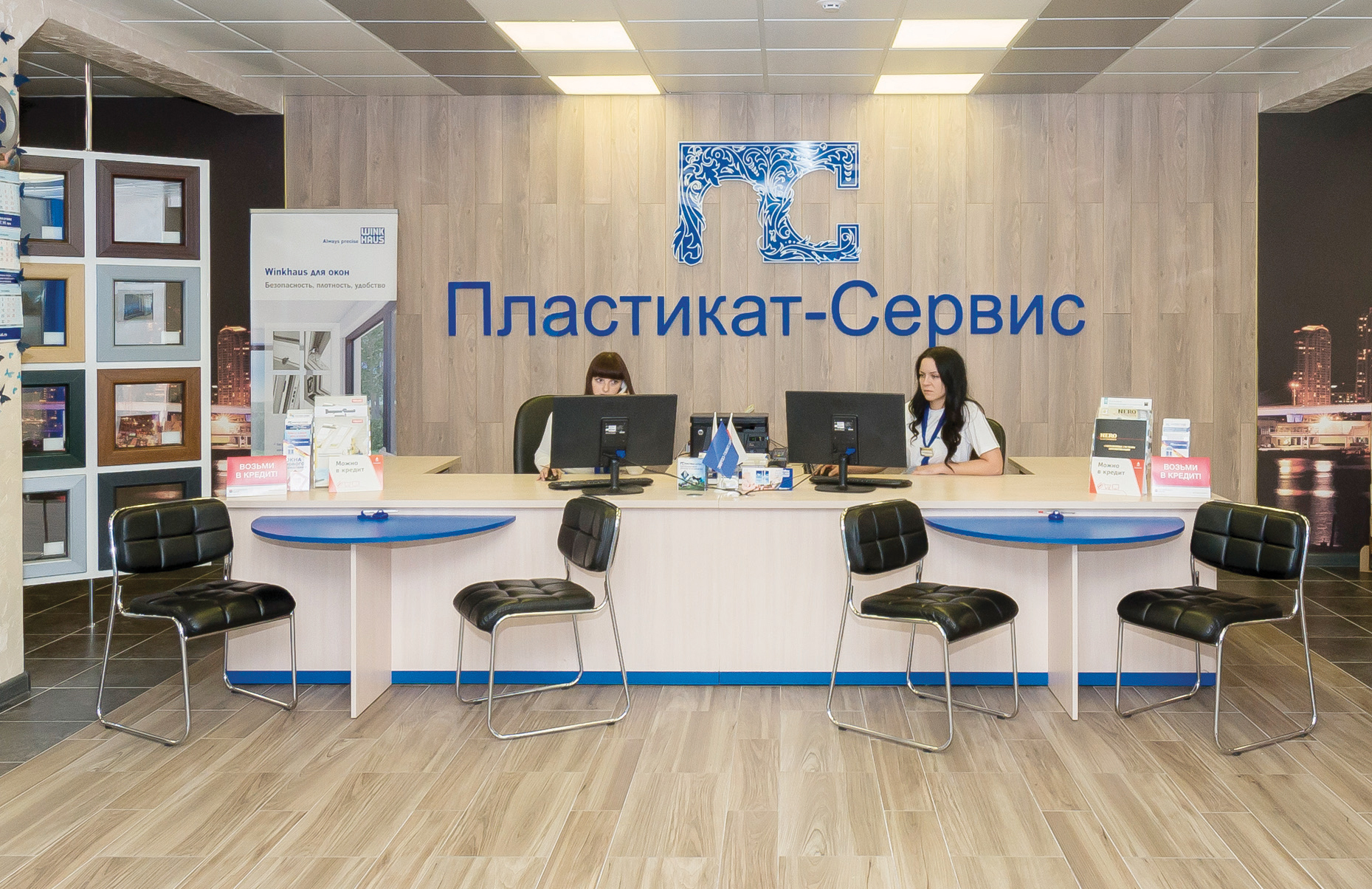
При заводе работает выставочный центр.